Ito Seisakusho’s policy for technology development
- Challenges faced by developers, designers, and manufacturers
- Ito Seisakusho’s strength in resolving challenges
- Research and development capabilities
- Technical prowess
- Equipment capabilities
- Quality strengths
- Human resources strengths
- Challenge spirit
- Trial and error approach
- Improvement of technology development and technical capability
- Towards creating new value-added products
Examples of technology development
- Shear technology
- Bending technology
- Drawing technology
- Plate forging
- Case of system development
Shear technology
Year 1992
Thirty years ago, when die materials, lubricants, and coatings were not as superior as they are today, we succeeded in mass-producing detents with minimal shear droop using precision shearing technology.
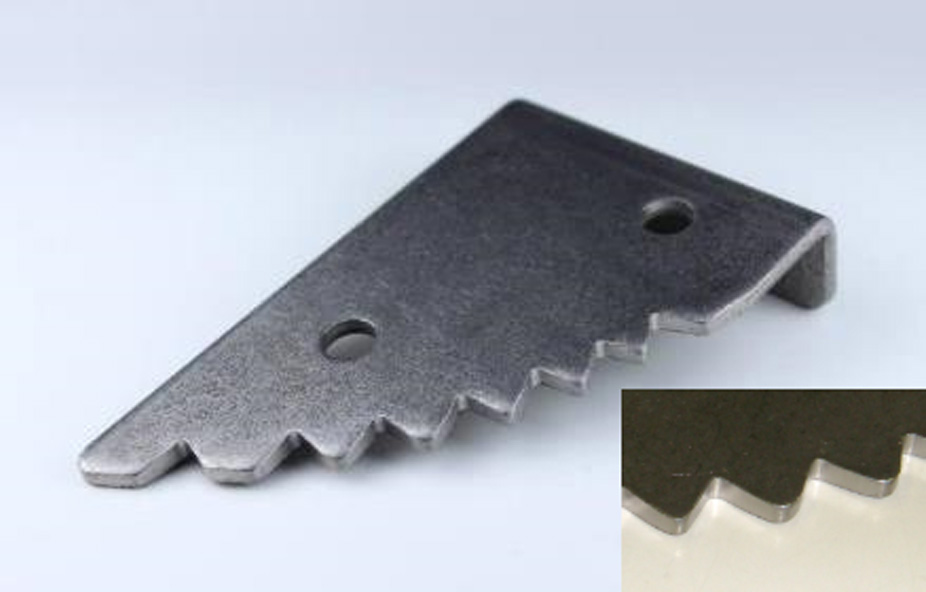
Equipment | 200-ton crank press |
---|---|
Product name | Dentent plate |
Material | SPHC (hot-rolled steel sheets) |
Thickness | 3.2mm |
Year 2000
Hinge component for a folding mobile phone. Forming side walls with width of 0.45mm while maintaining a shearing length of 1.5mm on a 2mm plate through sequential progressive pressing.
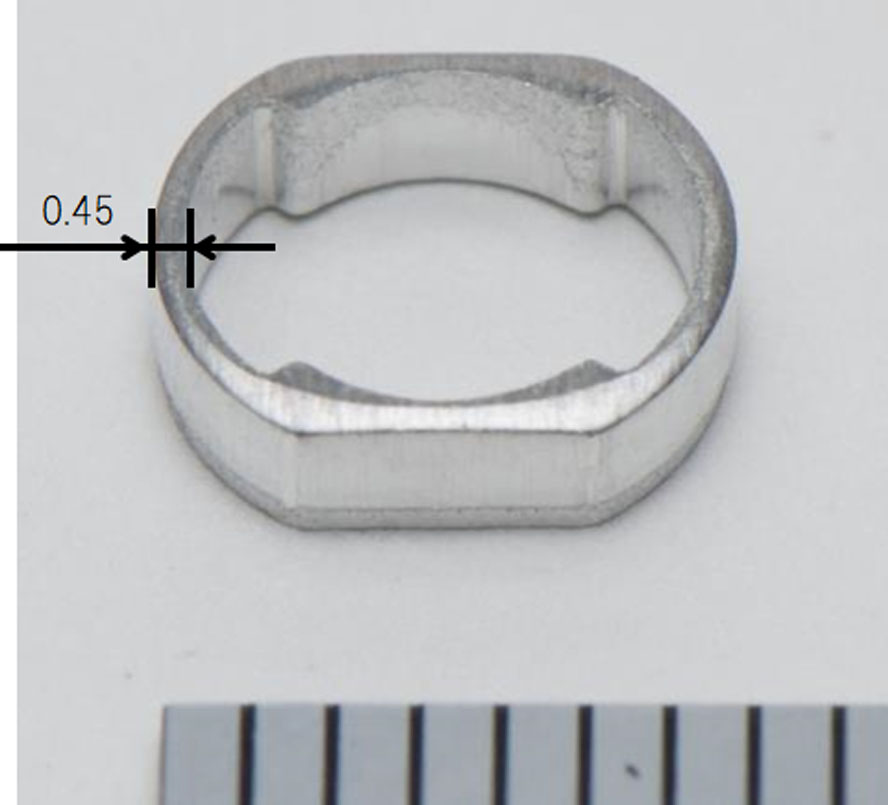
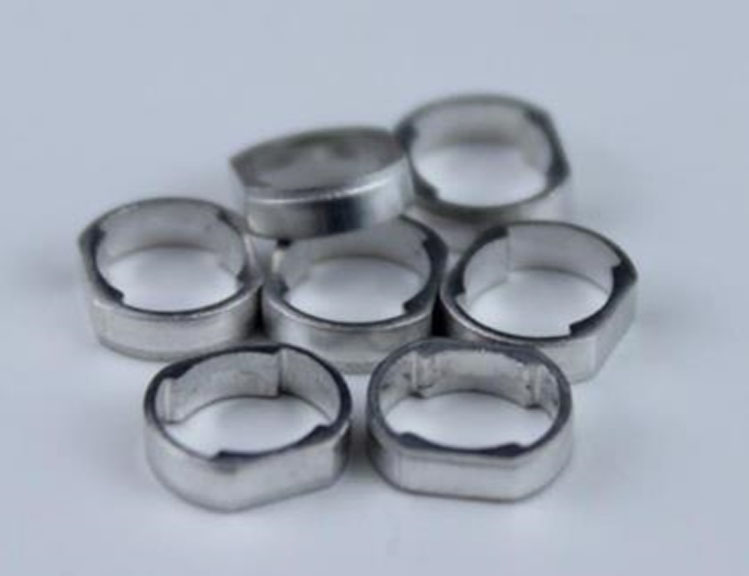
Equipment | 60-ton crank press |
---|---|
Product name | Insert nut |
Material | A5052-O |
Thickness | 2.0mm |
Year 2006
We challenged the narrow hole punching, which has been impossible by stamping and succeeded in punching a narrow hole with a hole diameter of 1.2 mm for a thickness of 6 mm.
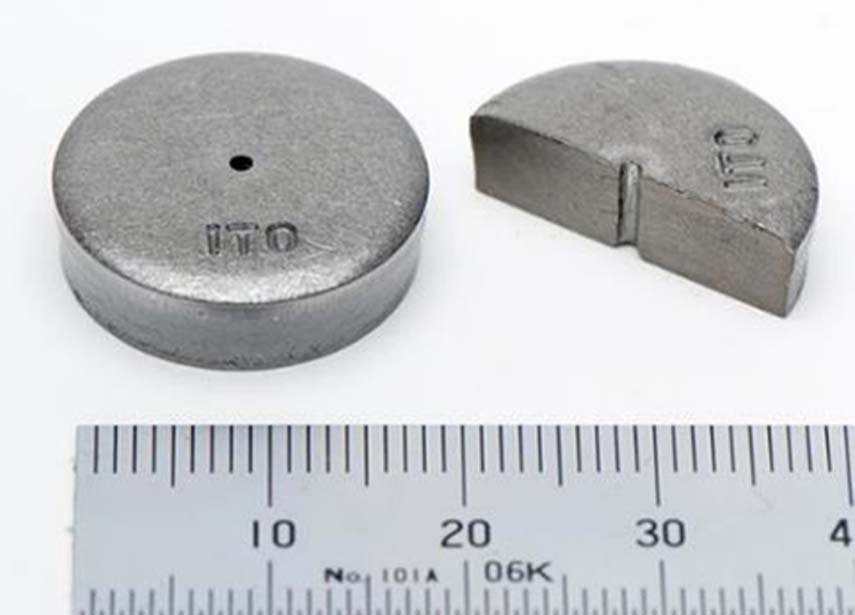
Equipment | 45-ton crank press |
---|---|
Product name | SPHC |
Material | 6.0mm |
Thickness | φ1.2 |
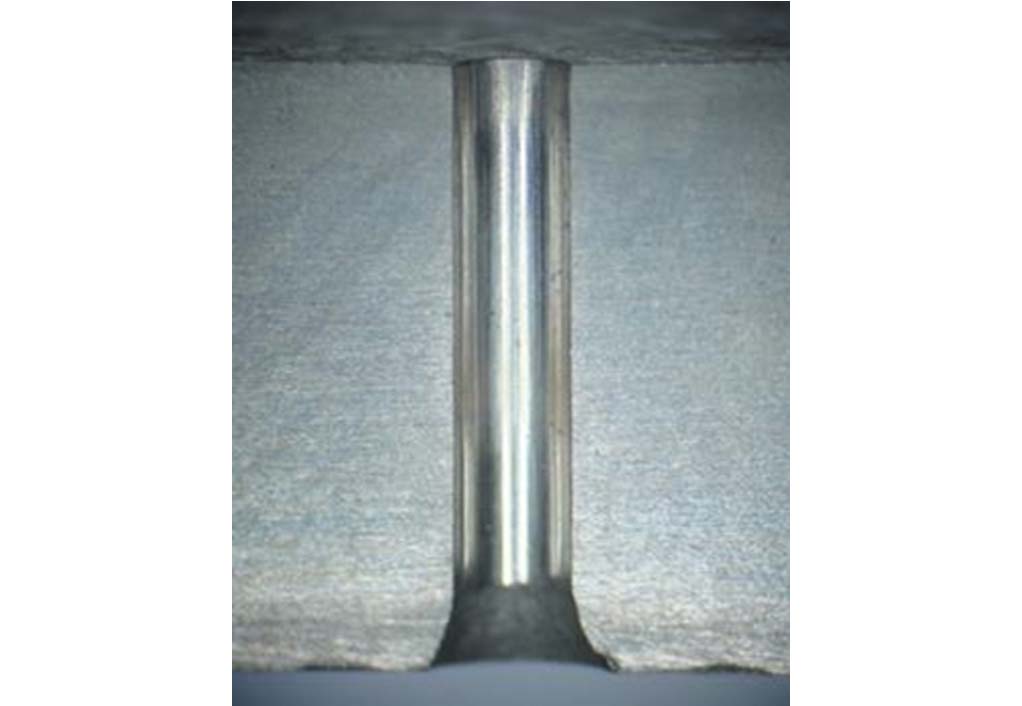
Drilling processing | ||
---|---|---|
Equipment | Machining | 45-ton press |
Tooling cost | ¥2,030 | ¥1,410 |
Tool life | 250 holes | 35000 holes |
Processing time | 18 seconds | 1 second or less |
Year 2007
The wall thickness is reduced to 50% of the thickness of 5.0mm, with a width of 2.5mm. Normally, such punching would result in a twisted section, but through the development of a special processing method, more than 75% of both the inner and outer diameter sections are ensured.
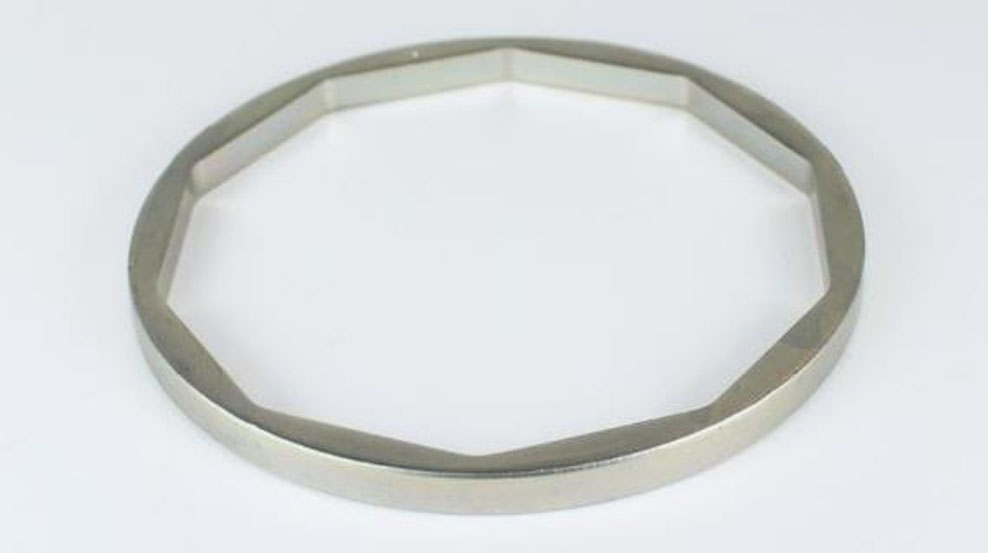
Equipment | 300-ton high-rigidity press |
---|---|
Product name | Nut starter |
Material | SPH270C |
Thickness | 5.0mm |
Outer diameter
Inner diameter
Year 2012
Converted from fine blanking to progressive press processing for sector gears used in sheet lifters. The conventional method reduced the shear droop from more than 1.5 mm to less than 0.5 mm for a thickness of 6mm and secured 90% of the shear surface length.
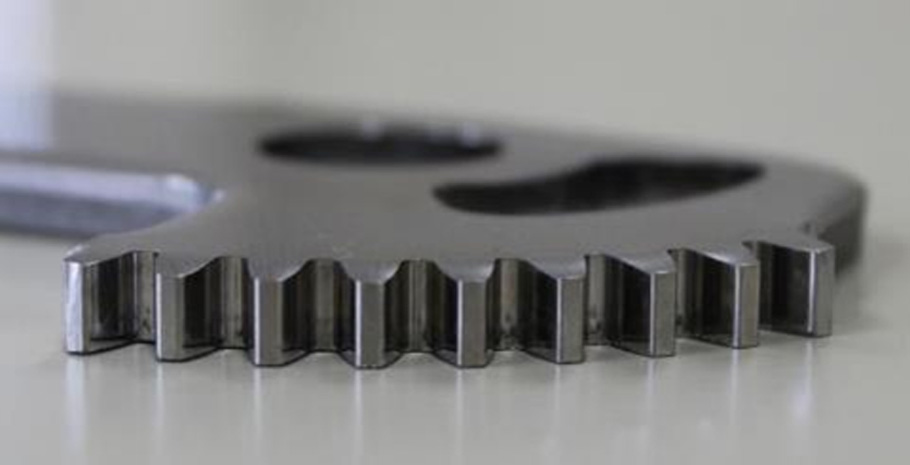
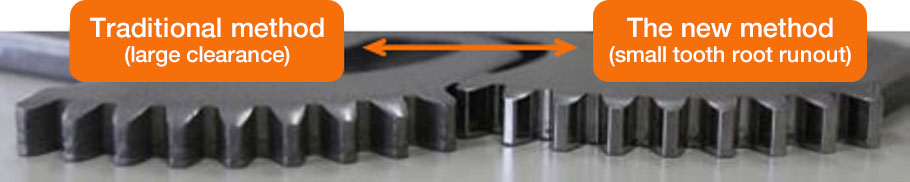
Our progressive press products.
Thickness 6.0mm
Deflection 0.5mm
Less than 10% of thickness
Equipment | 300-ton knuckle link press |
---|---|
Product name | Sector Gear |
Material | SCM415 |
Thickness | 6.0mm |
Year 2014
Enables single-stroke punching without matching the contours of a narrow peninsula shape while maintaining die strength. Reduces the number of processes and improves punching accuracy.
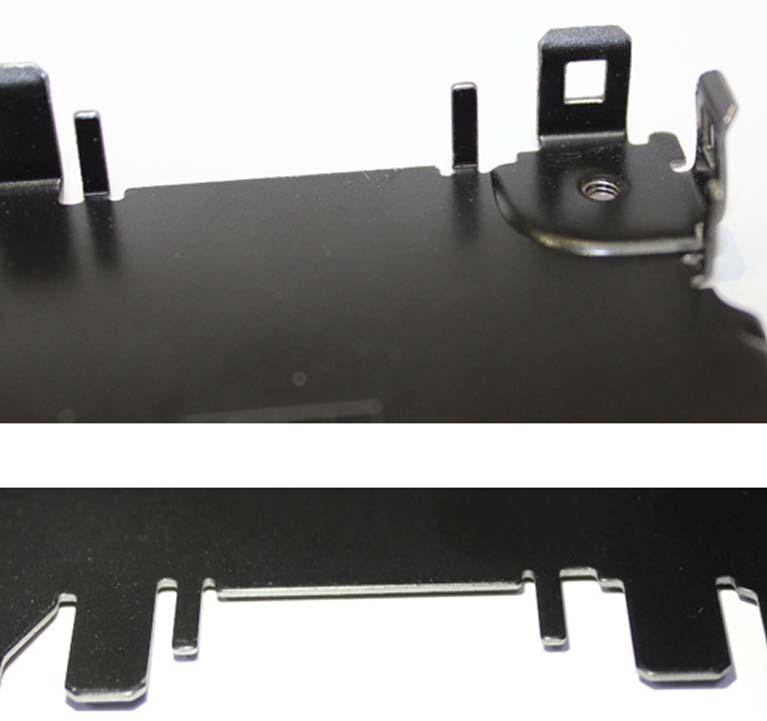
Equipment | 110-ton press |
---|---|
Product name | Base |
Material | SECC stands for Electro-Galvanized Steel with a Cold Rolled Base, which is a type of heat-dissipating coating Material. |
Thickness | 0.8mm |
Year 2016
The customer’s need for precision shear processing was gradually applied to thicker materials, and the company succeeded in precision shearing of 7.2 mm Thickness By pressing all fine holes with a press, the turning time in the subsequent process was drastically shortened.
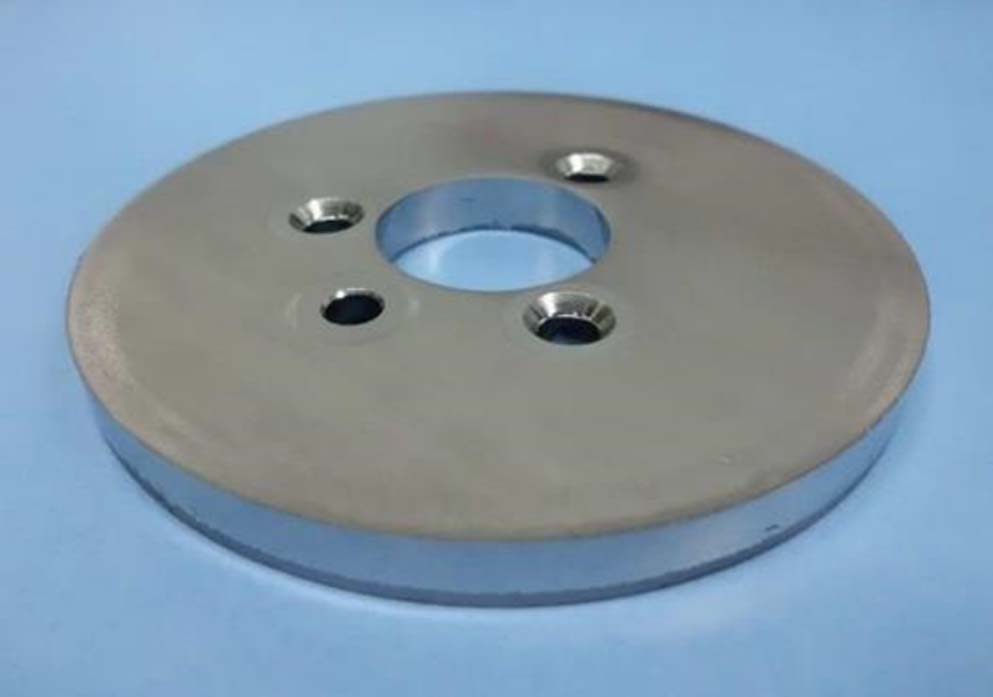
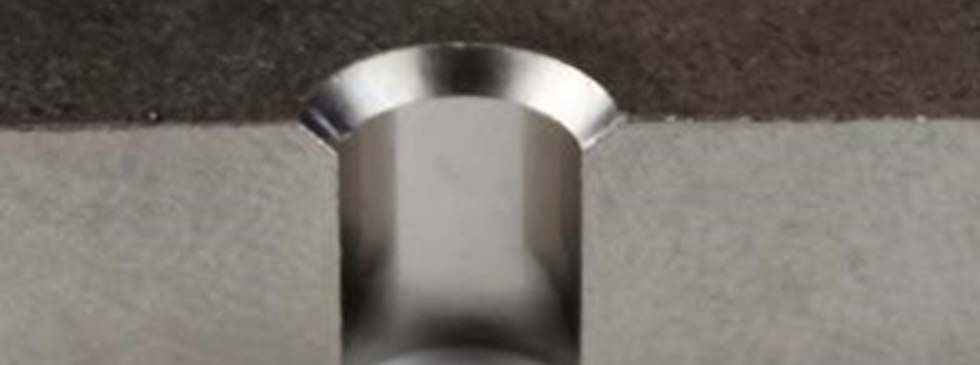
Equipment | 400-ton knuckle link press |
---|---|
Product name | The base Material |
Material | SPH440C |
Thickness | 7.2mm |
Year 2020
Previously, the sector gear for sheet lifter was produced using fine blanking, but the production method was changed to sequential press processing. By controlling the shear droop to less than 0.2mm and ensuring a shear surface length of 90% or more, the accuracy was improved.
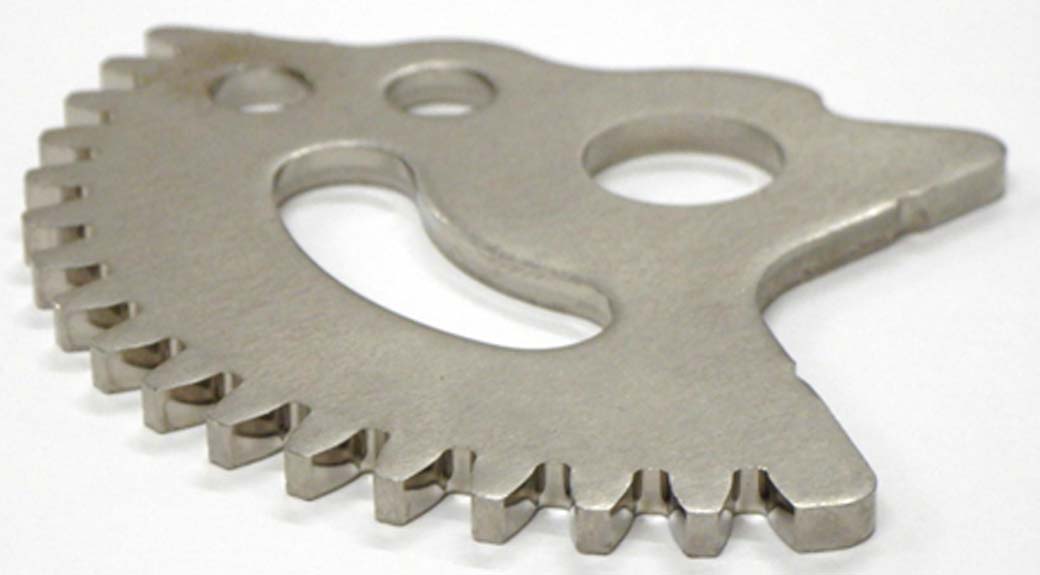
Equipment | 200-ton servo press |
---|---|
Product name | sector gears |
Material | SAPH440 |
Thickness | 3.2mm |
Module | 2 |
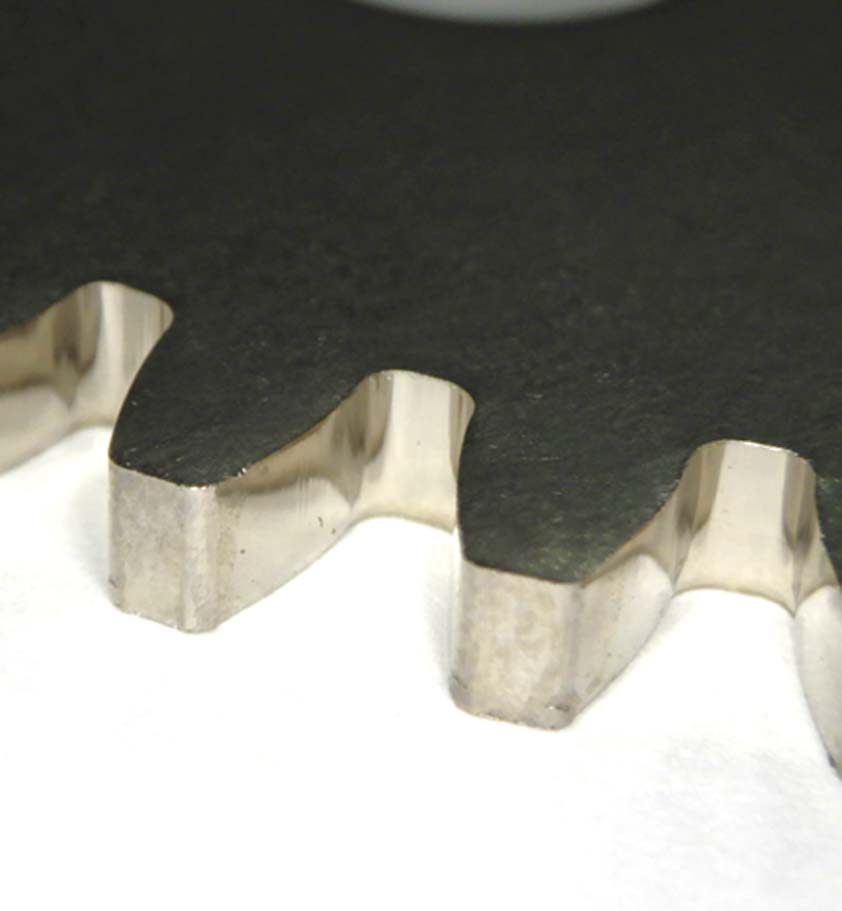
Bending technology
Year 1999
With the spread of Windows 95, we succeeded in mass production of the rotor yoke of floppy disk drives, which began ultra-mass production. Since an accuracy of 5 microns was required, such as shaft diameter tolerances, runout, and flatness, the dimensional accuracy of mold parts was finished with sub-microns.
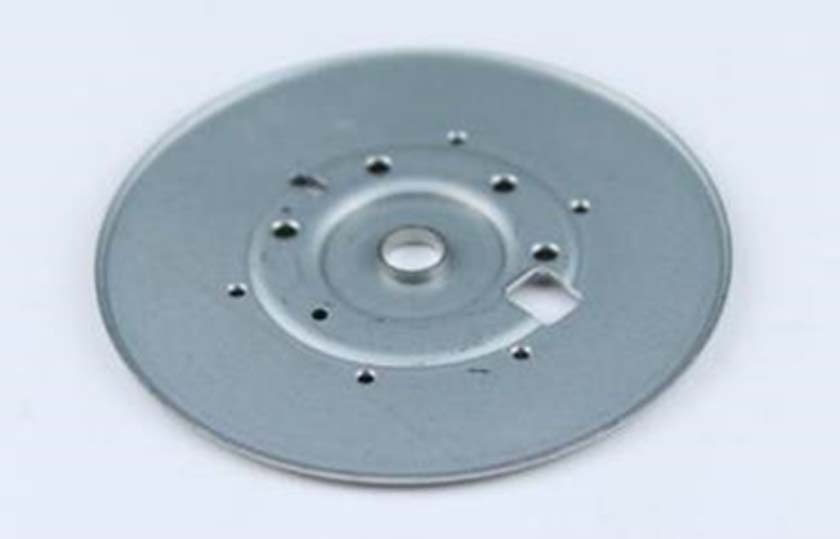
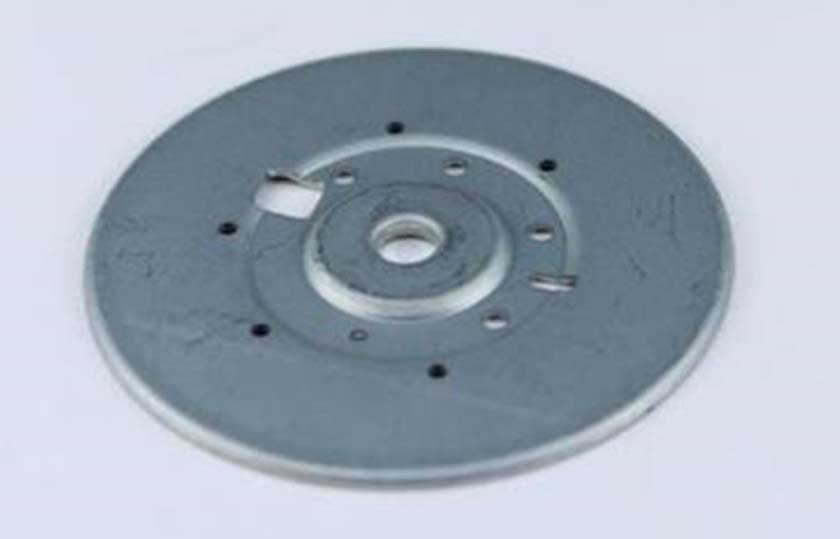
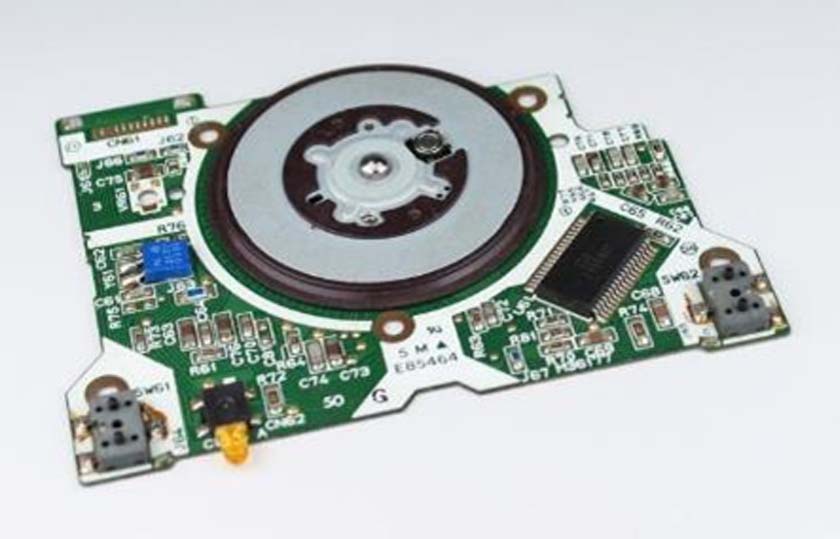
Equipment | 110-ton high-speed press |
---|---|
Product name | Rotor yoke |
Material | EGC-E20/20 |
Thickness | 0.6mm |
Year 2009
Using the technology of overlapping plates without cutting, we have succeeded in the progressive press working of key holders.
Moreover, a fine hole of 0.5 mm dia. is produced for a thickness of 1.6 mm.
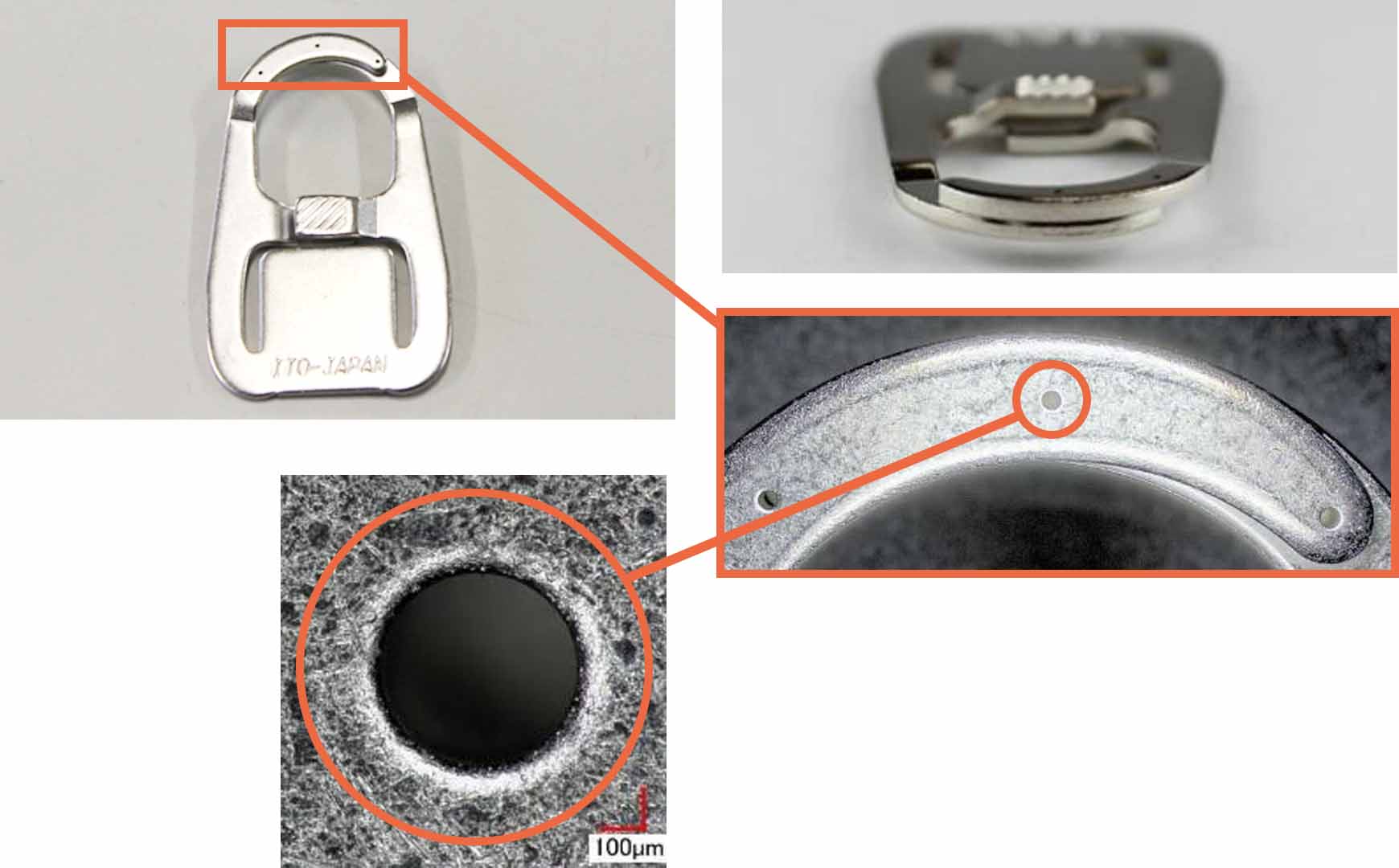
Equipment | 100-ton high-speed press |
---|---|
Material | C2680-1/2H |
Thickness | 1.6mm |
Year 2017
BEFORE: With the crank press, the spring back varied, and adjustment of the correction process was necessary when the material was changed.
AFTER: The servo press succeeded in reducing the spring back variation by slowing down during the bending process and stopping for 0.2 seconds at the bottom.
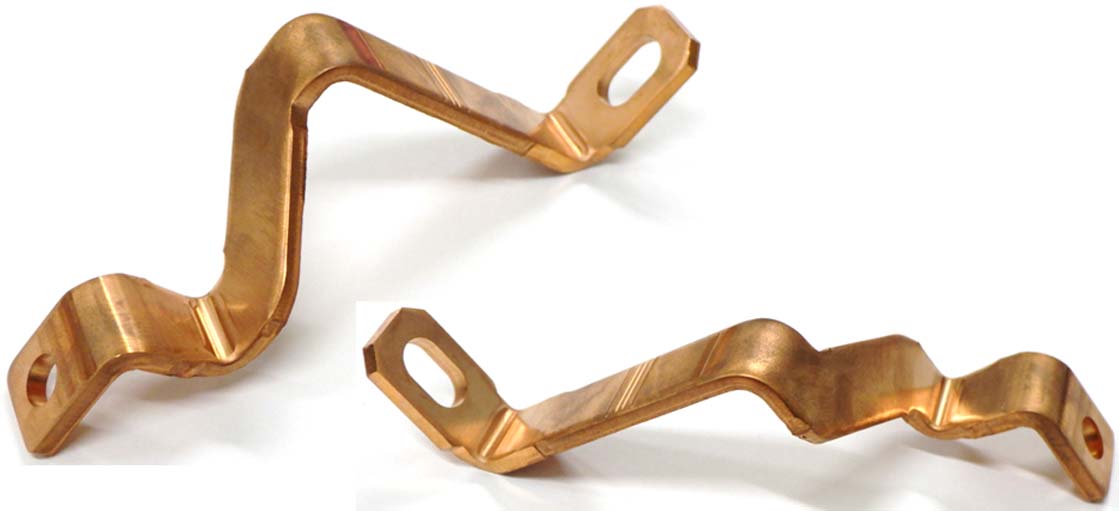
Equipment | 200-ton servo press |
---|---|
Product name | Busbar |
Material | C1020-H |
Thickness | 3.0mm |
Drawing technology
Year 1995
Stainless steel square drawing parts narrowed down to 16 x 8 x 50 in height in 7 processes.
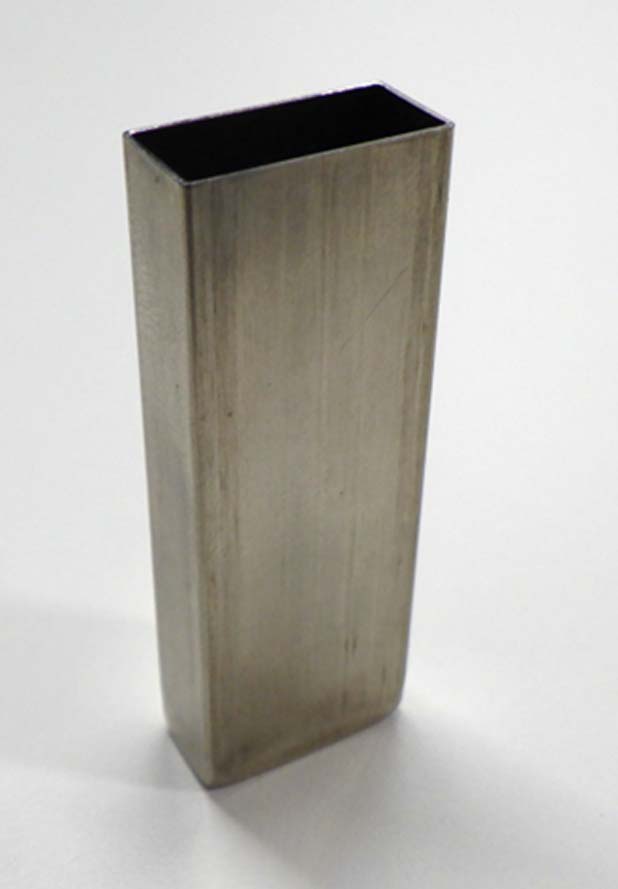
Equipment | 110-ton press |
---|---|
Product name | Battery case |
Material | SUS304 |
Thickness | 0.4mm |
Year 2003
Outer ring part of seat lifter clutch. The inner diameter dimension after carburizing, quenching, and tempering is controlled at ±0.02.
Used by all but one Japanese automaker; total production of 100 million units was recorded in 2017.
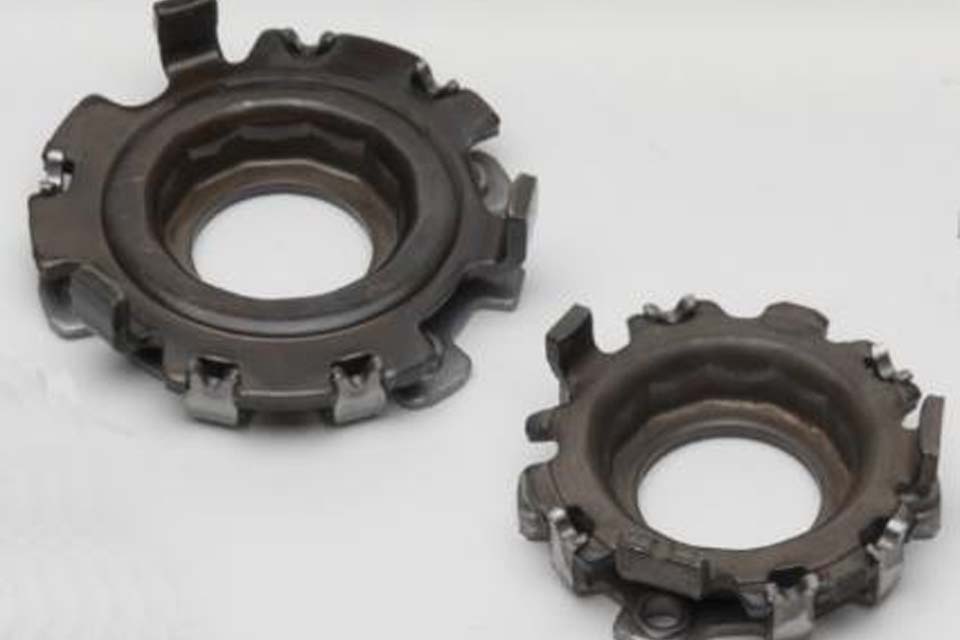
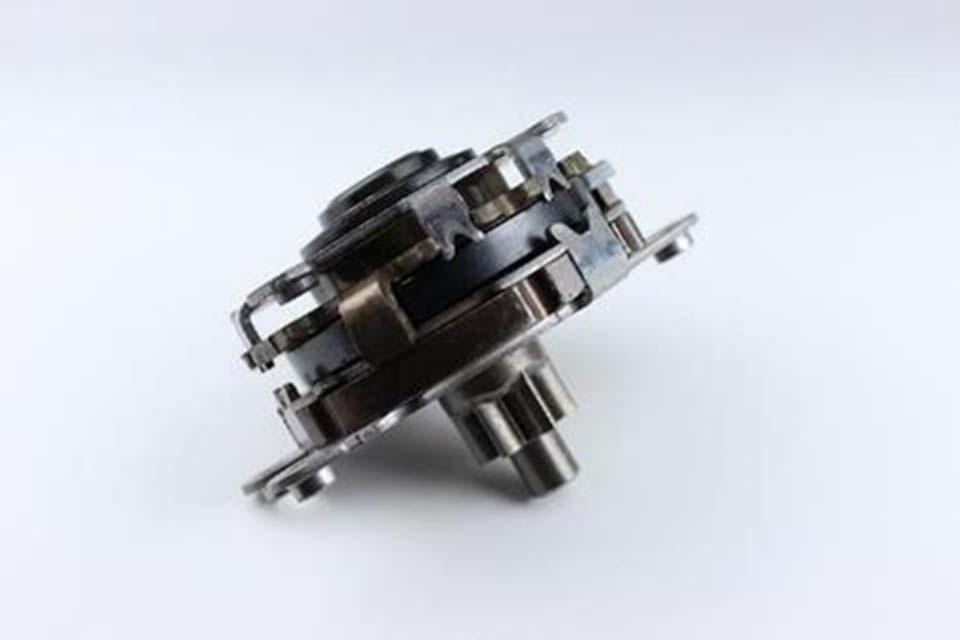
Equipment | PMX-3000 |
---|---|
Product name | Outer ring |
Material | SCM415 |
Thickness | 2.9mm |
Year 2015
Stainless steel deep-drawn parts. Due to quality requirements, the process is designed to avoid local deformation as much as possible and to achieve homogeneity.
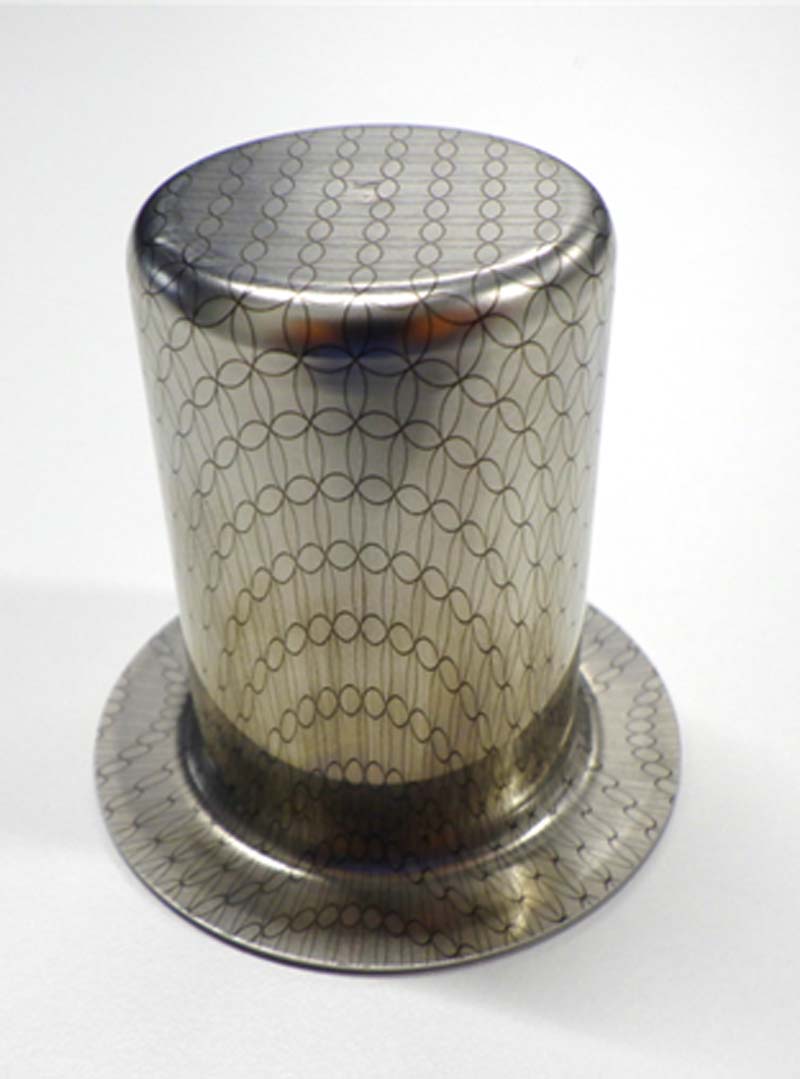
Equipment | 150-ton servo press |
---|---|
Product name | Case |
Material | SUS304 |
Thickness | 0.5mm |
Year 2020
The case of the sheet lifter clutch. Precision drawing of high-tensile Material The mold has 24 steps and the length is 2300mm.
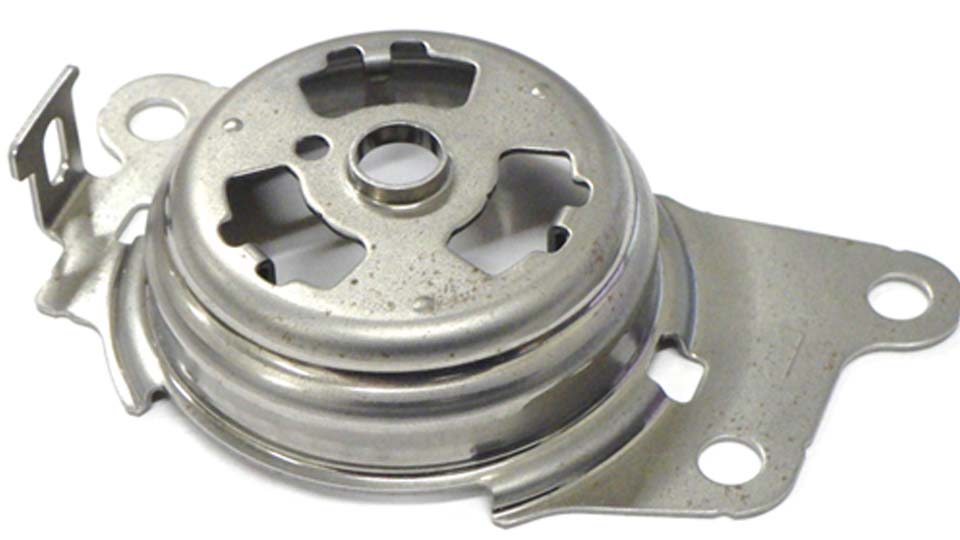
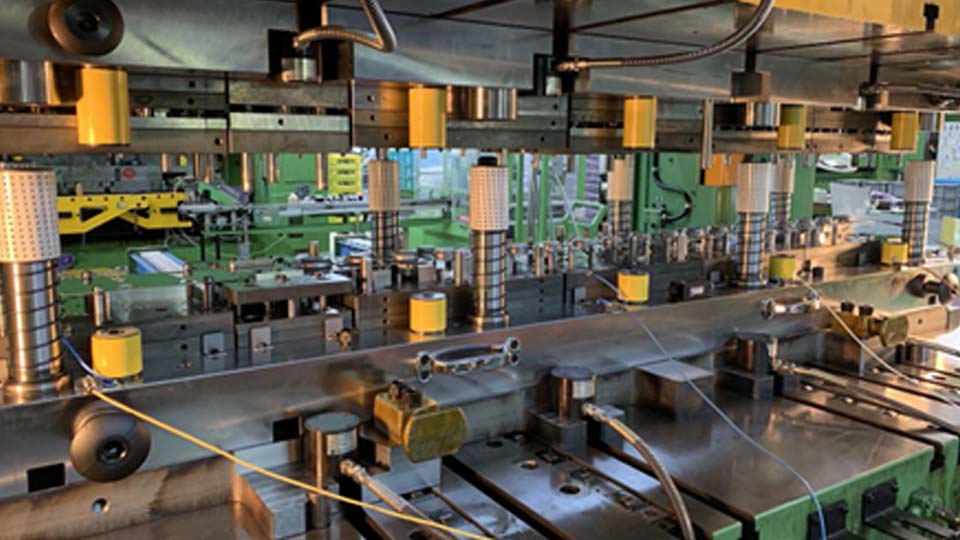
Equipment | PMX-6000 |
---|---|
Product name | Case |
Material | SPC590 |
Thickness | 1.0mm |
Plate forging
Year 1995
Our company has been mass producing plate forging and precision cutting. These have become widely popular in Japan, since the 1990s by incorporating them into progressive dies.
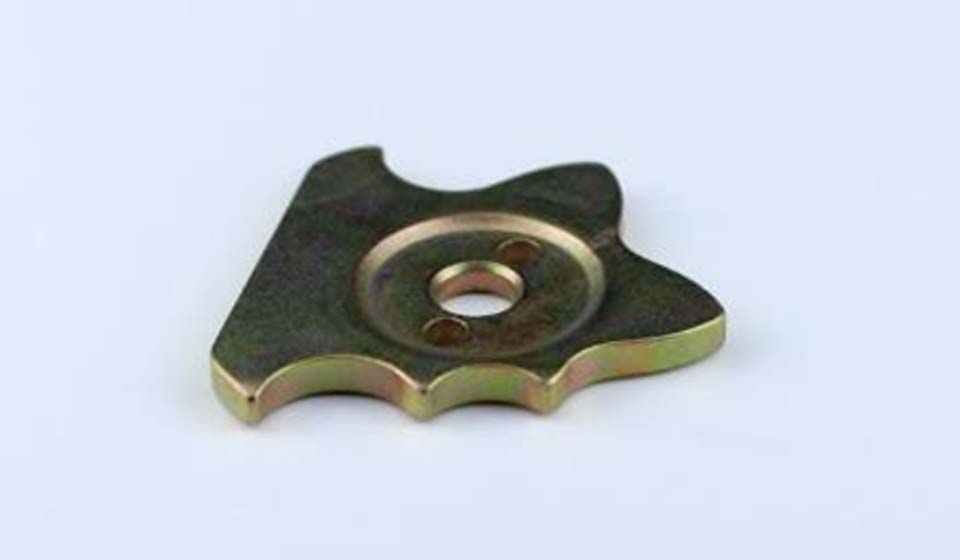
Equipment | 150-ton link press |
---|---|
Product name | Shift drum |
Material | SPCE |
Thickness | 3.2mm |
Year 2008
The plate forging technology cultivated to date has been applied to the serration of the bottom butt and the integrated molding of the nut by progressive press working.
Our specialty, narrow-hole machining, is performed simultaneously at four locations in a progressive mold.
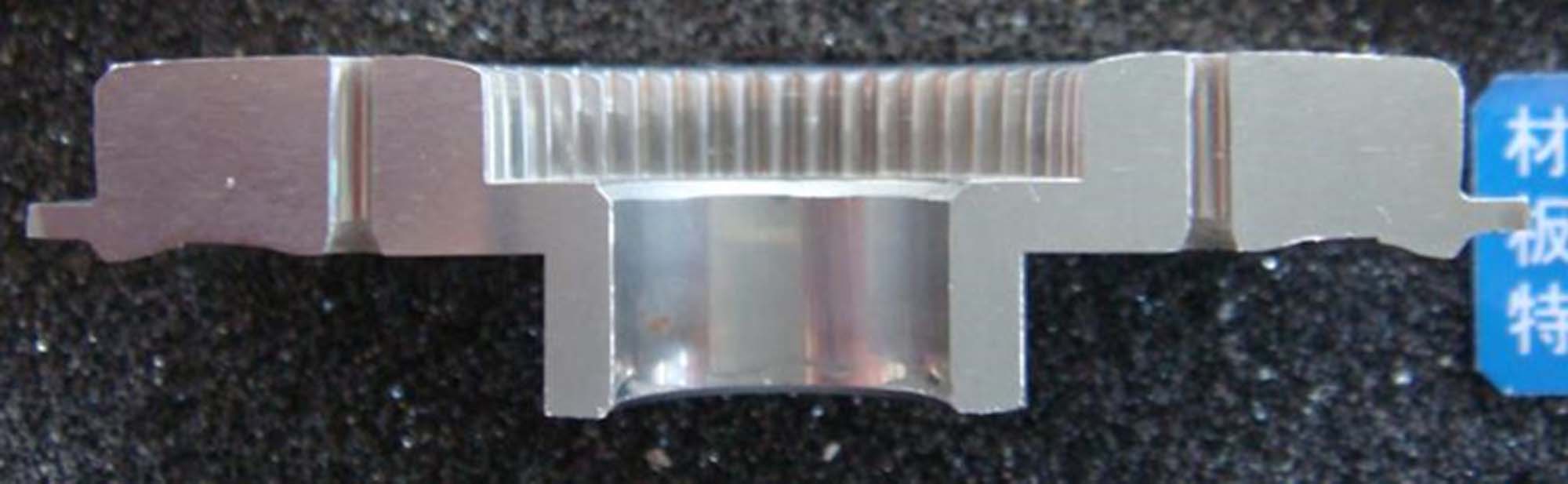
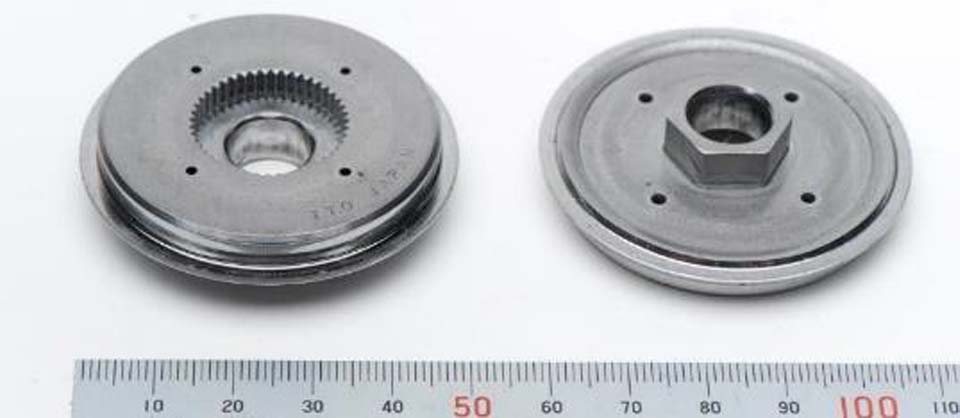
Equipment | 600-ton link press |
---|---|
Material | SPHC |
Thickness | 6.0mm |
Year 2010
Until now, our company has excelled in narrow hole drilling using shearing technology, but we have further succeeded in drilling narrow holes with a higher aspect ratio by combining shearing technology with plate forging technology.
The former was φ1.2 for a thickness of 6 mm, while the latter realized φ1.15 for a height of 7 mm.
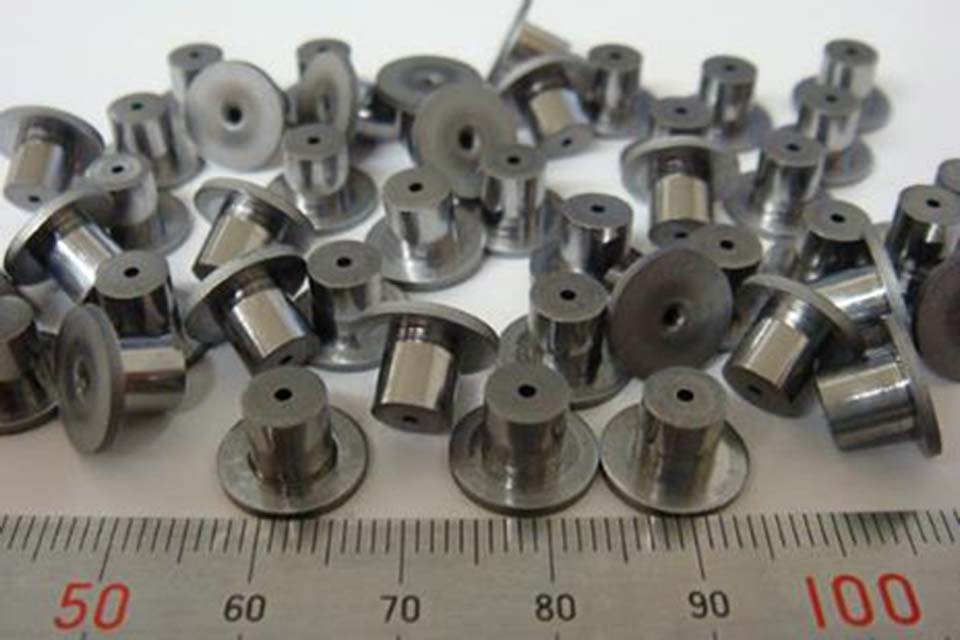
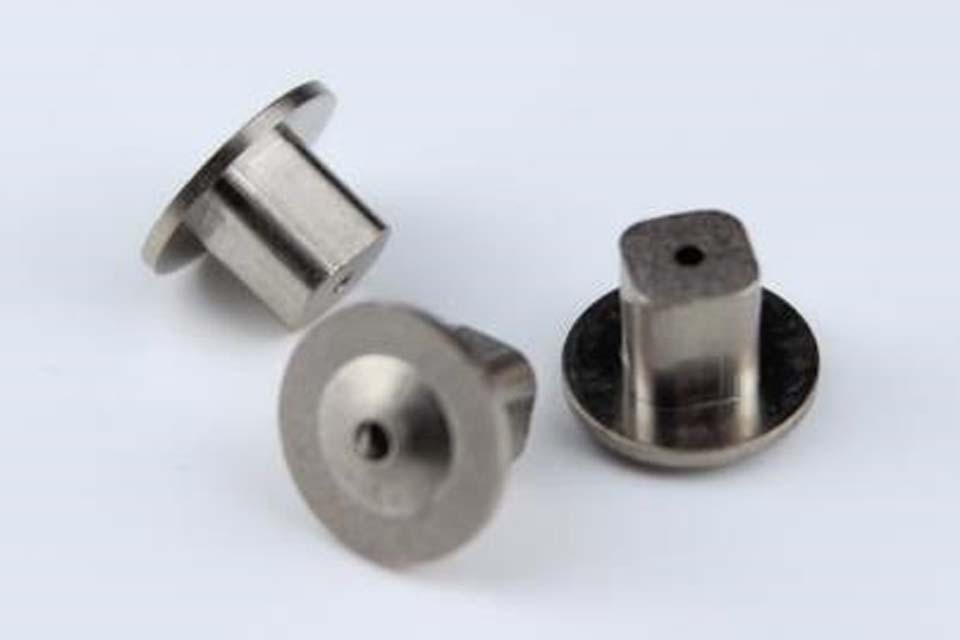
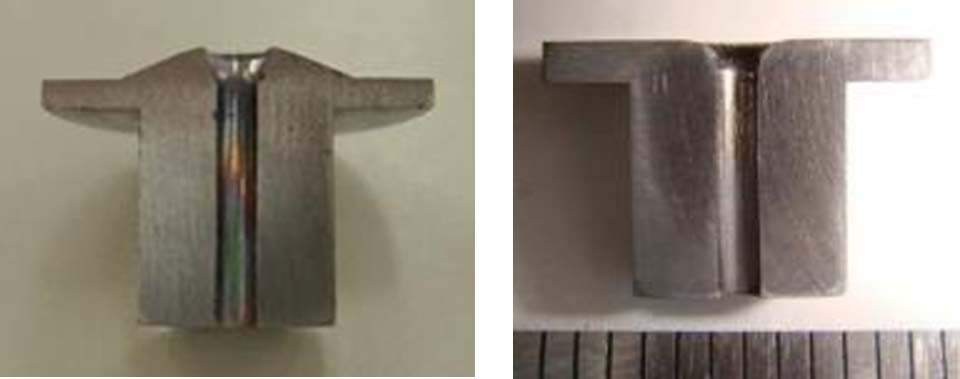
Equipment | 150-ton servo press |
---|---|
Product name | Nozzle |
Material | SPHC |
Thickness | 5.0mm |
Year 2011
Using a progressive press, we successfully mass-produced rivet integrally formed car air-conditioner clutch parts.
A Φ3.0, 5 mm high pin was formed by plate forging, and by making full use of precision shearing technology, a 2 mm wide slit punching and an outer diameter sheared surface of 80% or more were achieved for a thickness of 4.3 mm.
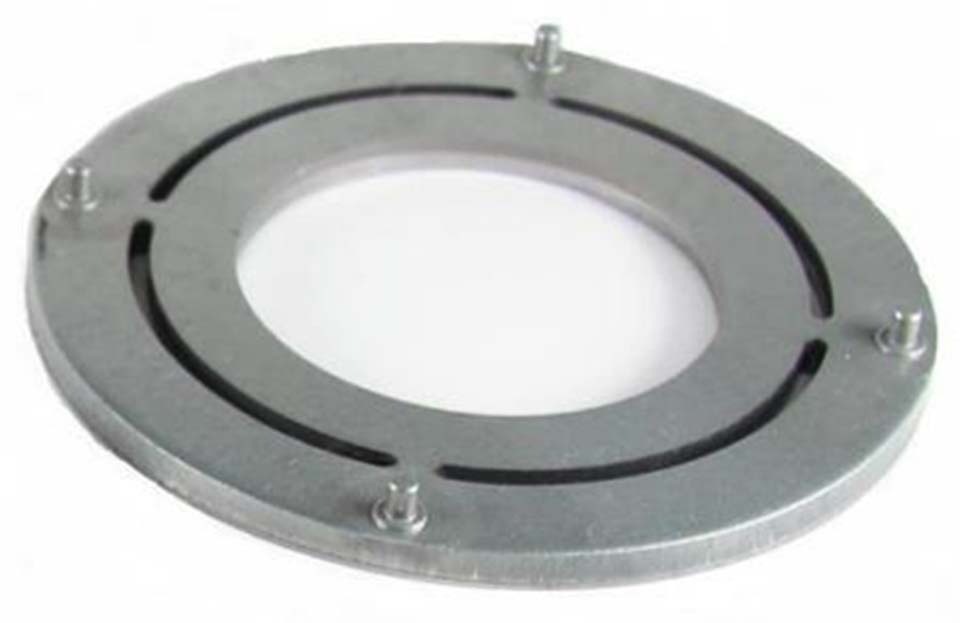
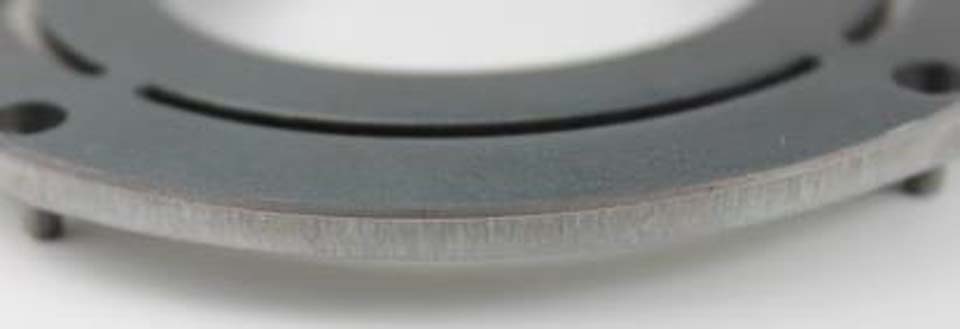
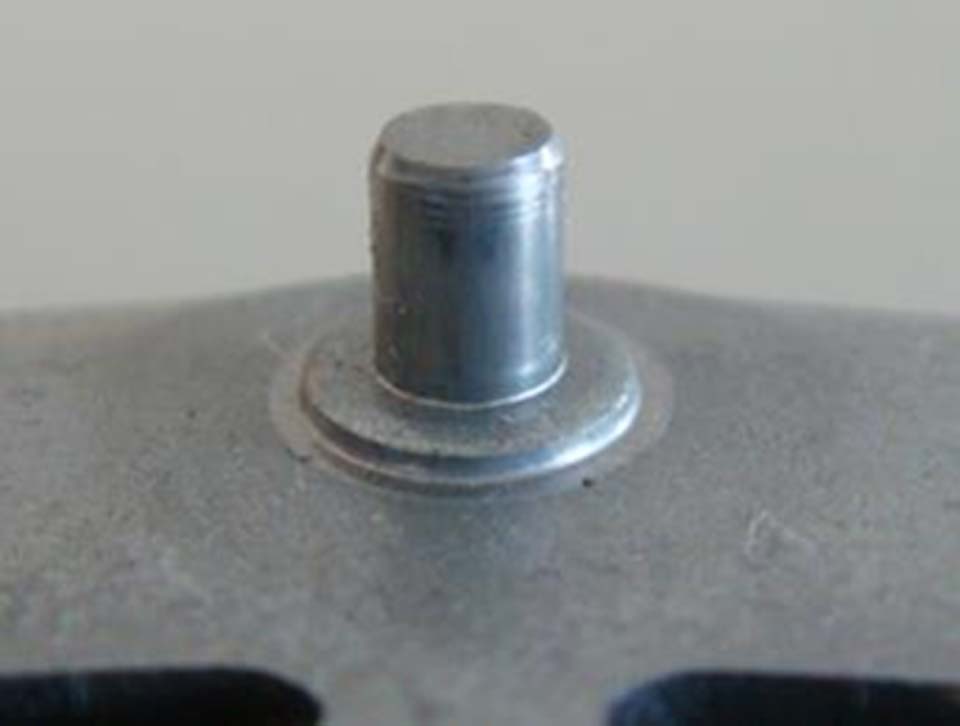
Year 2011
We have successfully created precise shapes for the upper and lower surfaces of the punching hole.
The surface roughness is controlled at Ra0.3 or less because it is necessary to seal the oil with a ball that comes in contact with the R0.7 part, and the height tolerance when the ball is placed is maintained at ±0.01.
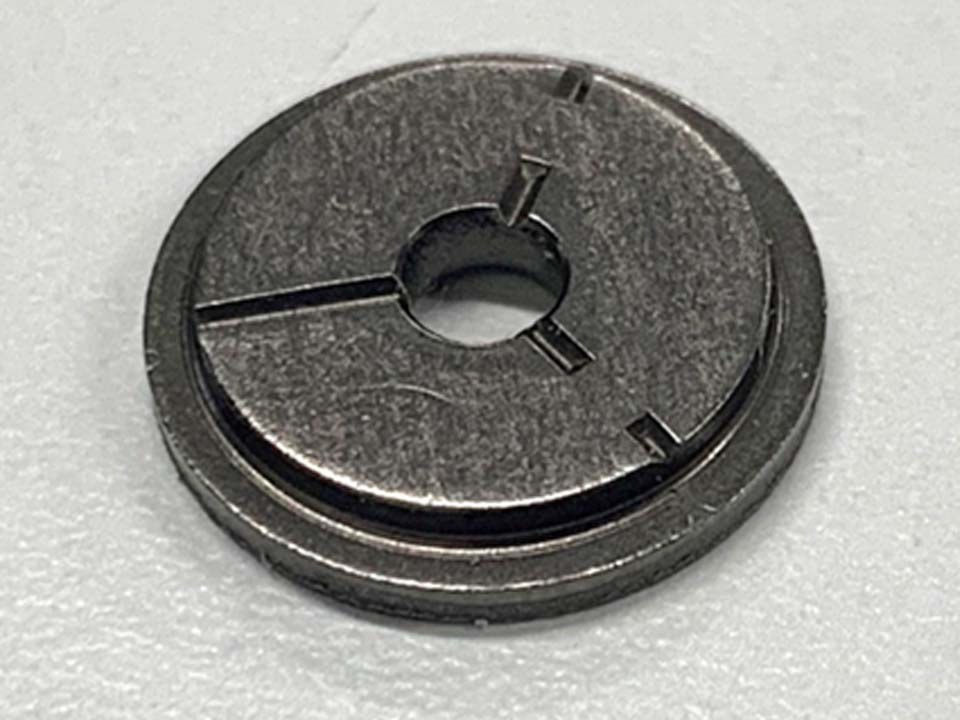
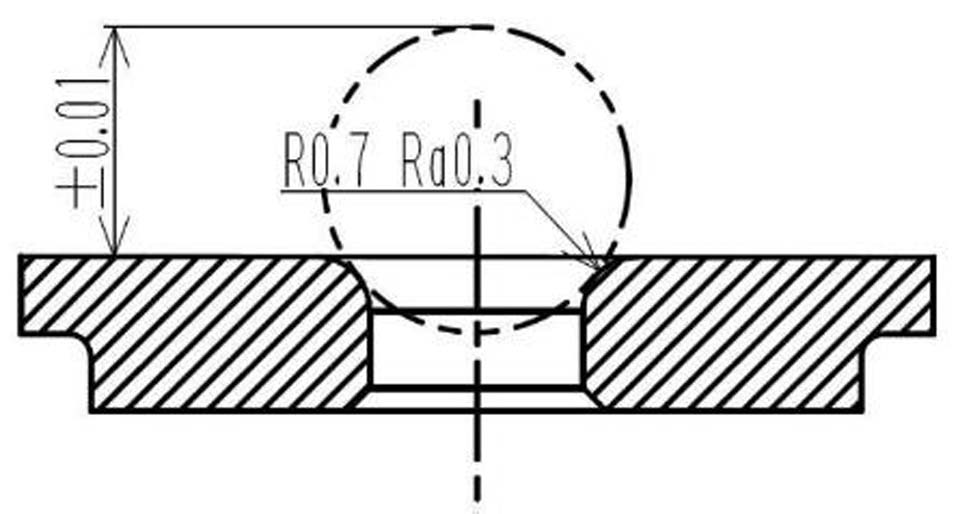
Equipment | 110-ton press (2 output) |
---|---|
Product name | Ball seat |
Material | SPHC |
Thickness | 2.0mm |
Year 2012
We have succeeded in simultaneous processing from both the front and back sides, which was difficult in the past. There is deviation on both sides and the thickness of the plate affects it.
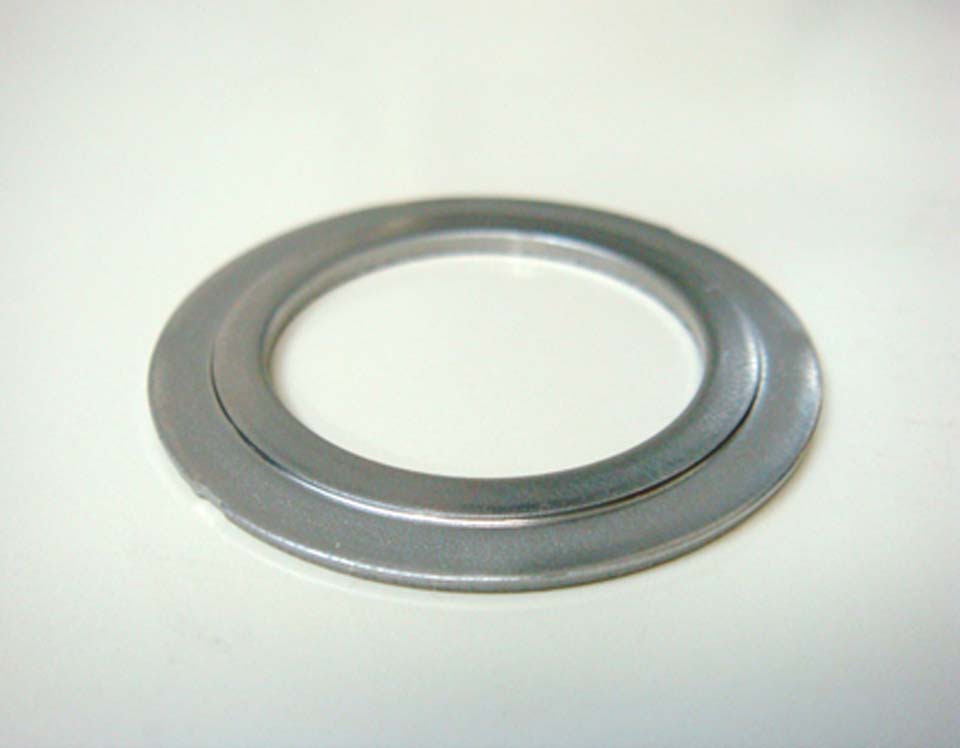
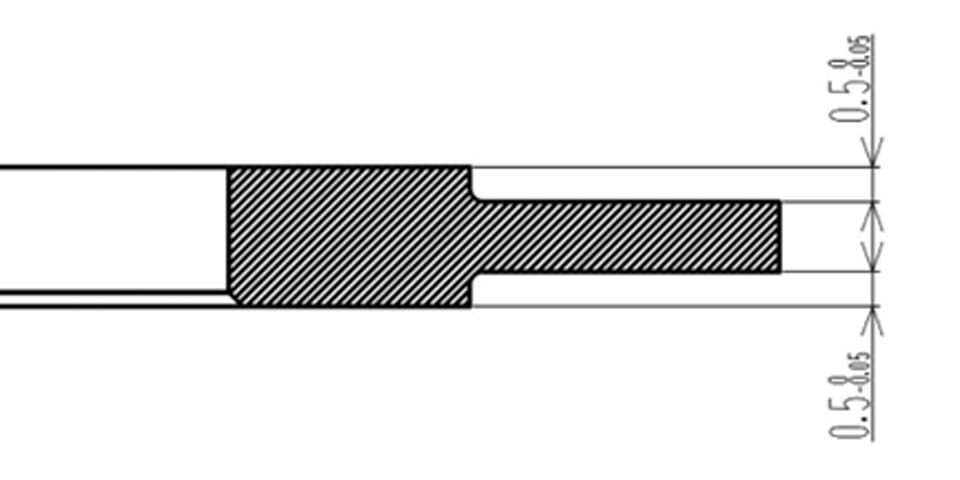
Equipment | 200-ton high rigidity press |
---|---|
Product name | Step washer |
Material | SPCC |
Thickness | 2.0mm |
Year 2018
The barring shape was formed by plate forging because a natural radius was not possible.
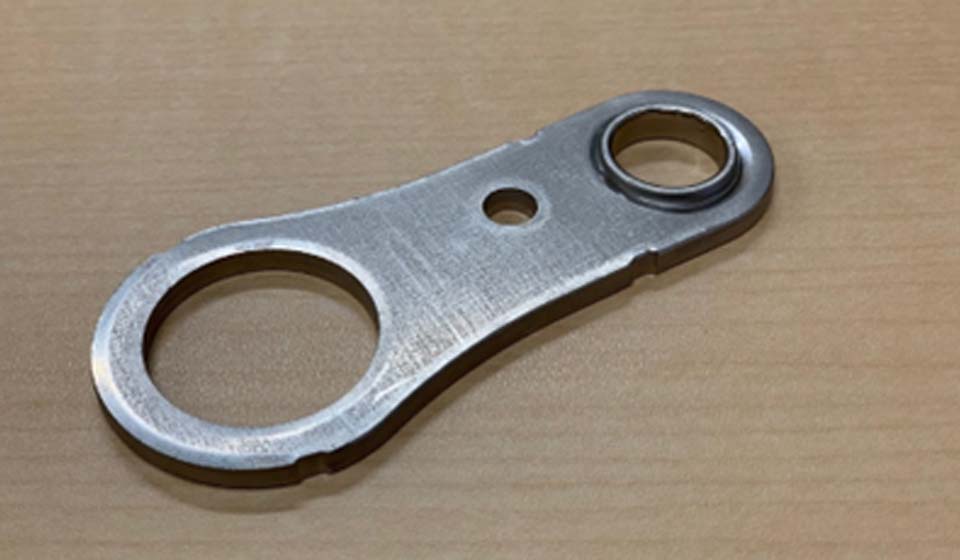
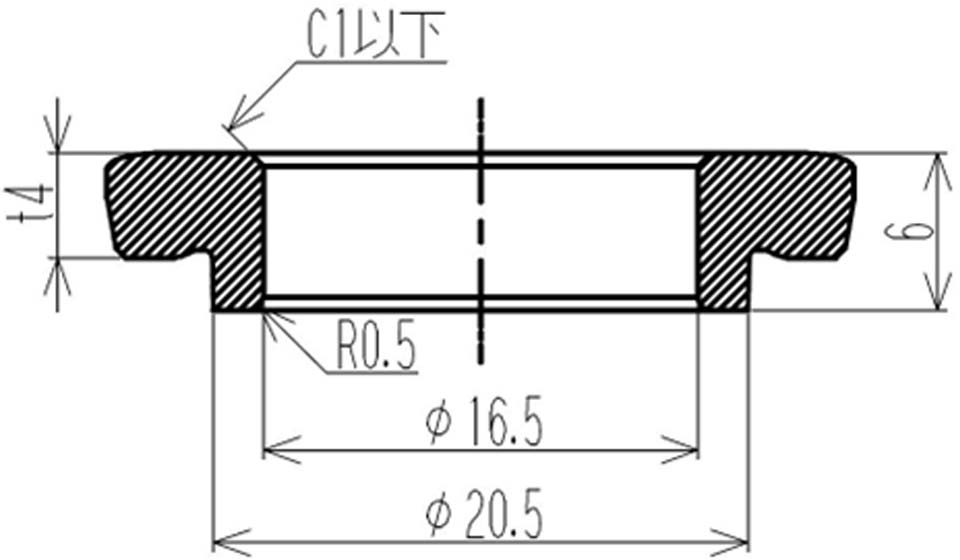
Equipment | 400-ton link press (2 output) |
---|---|
Product name | LINK, VERTICAL |
Material | SPH440-OD |
Thickness | 4.0mm |
Case of system development
Year 2015
Press Continuous Marking System
Our continuous marking system uses a laser marker. By laser marking the obtained information and identification number of each piece directly on the product, traceability, which used to be by lot or by box, can be traced down to the individual piece.
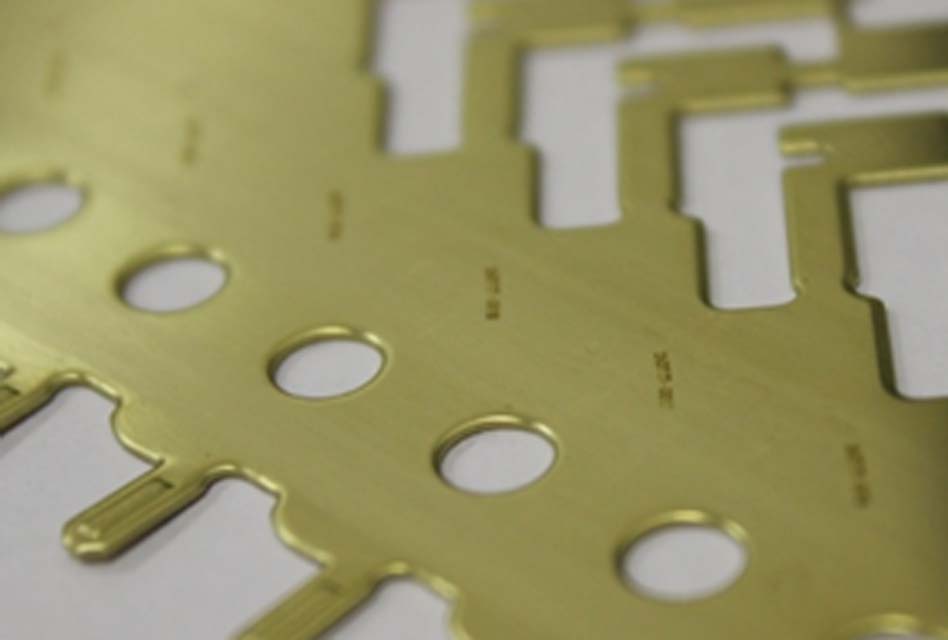
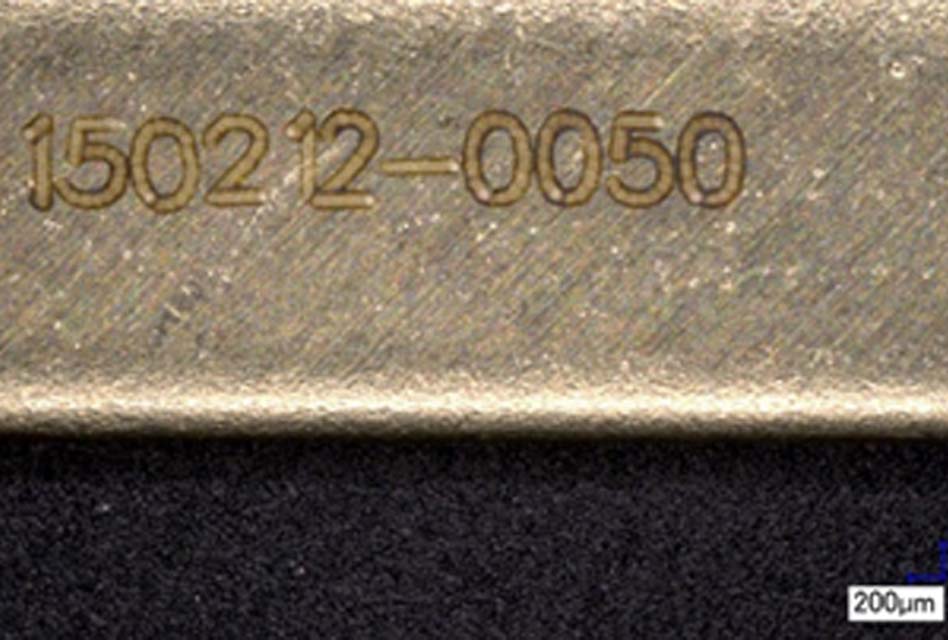
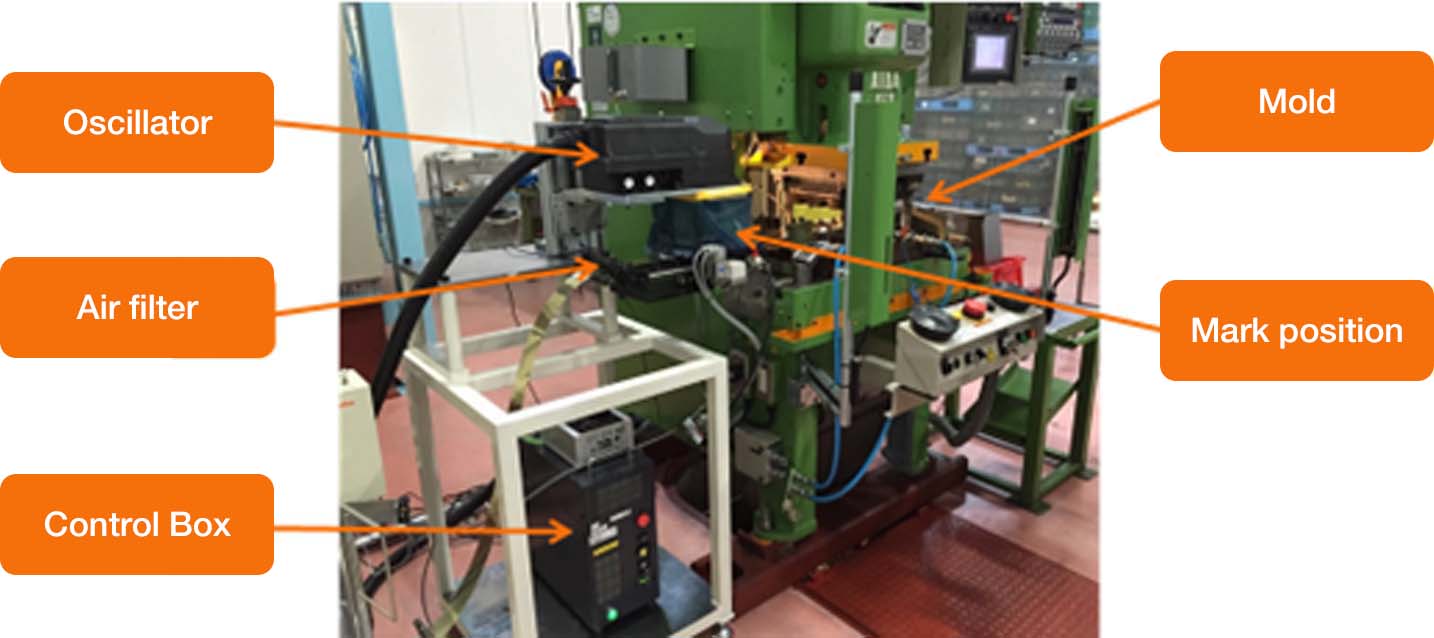
Year 2016
Scribed Circle Marking System
System for creating scribed circle data using a laser marker.
Scribed circles used to be created by stamping metal ink, but by drawing scribed circles with a laser marker, lines do not disappear even in multiple processes, and precise measurement is now possible.
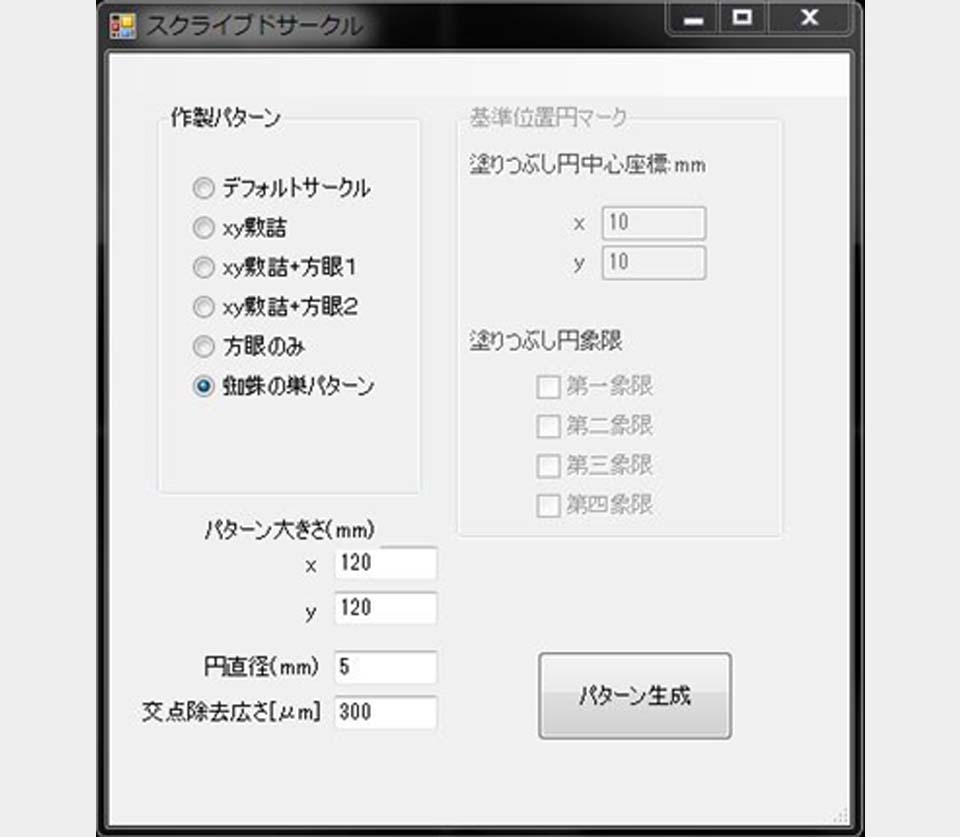
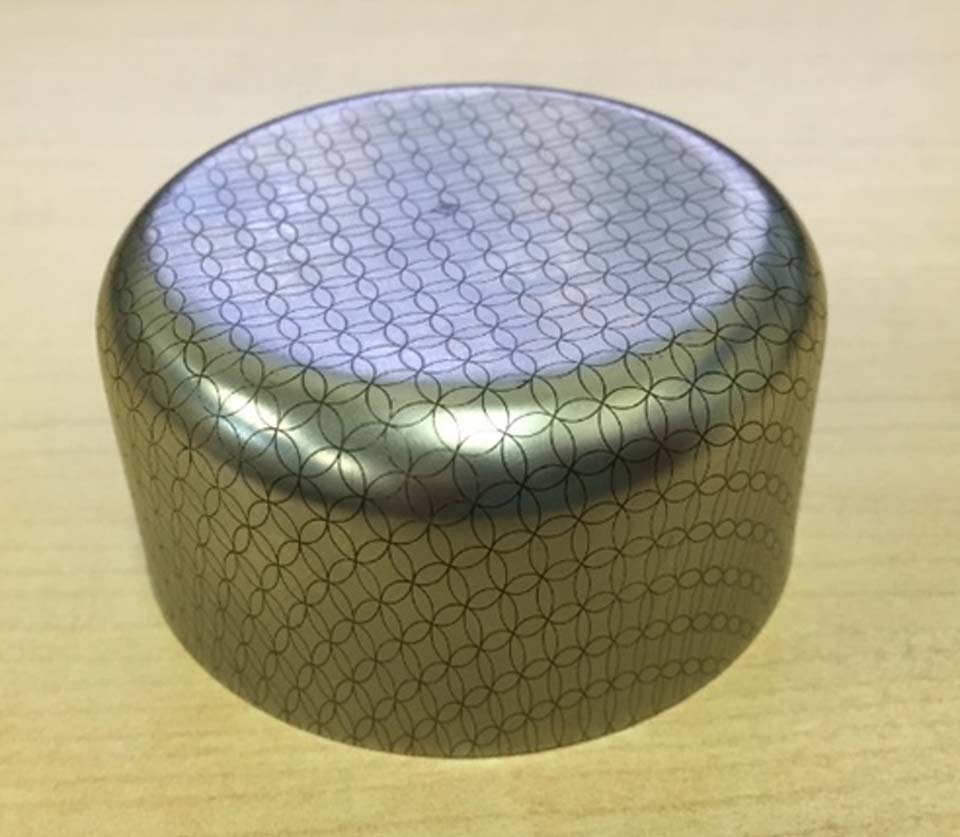
Year 2020
Press Sensing System – A system that uses sensors to monitor and control the processing conditions during press operations. The system helps to improve the quality and accuracy of press processing by continuously measuring and adjusting parameters such as temperature, pressure, and material Thickness
The operating dies are constantly monitored (sensing) and processed by an edge PC and simultaneously transferred to the cloud. Punch life prediction system using trend value management and Ai.
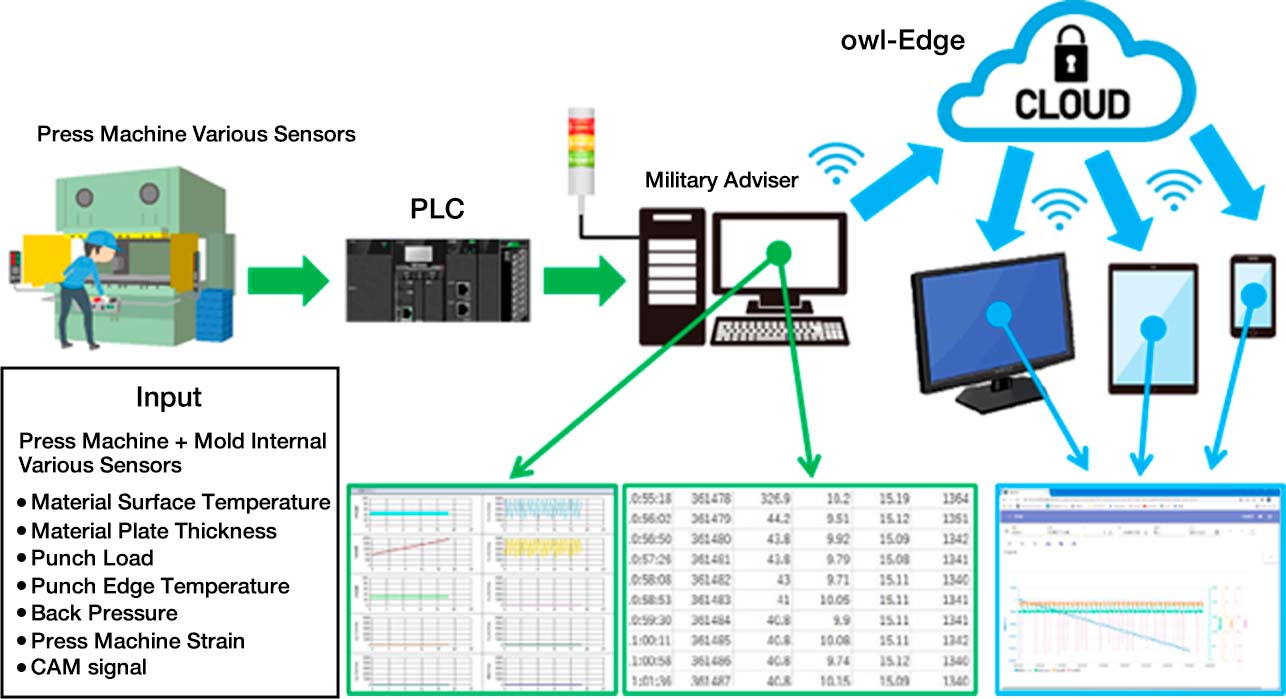
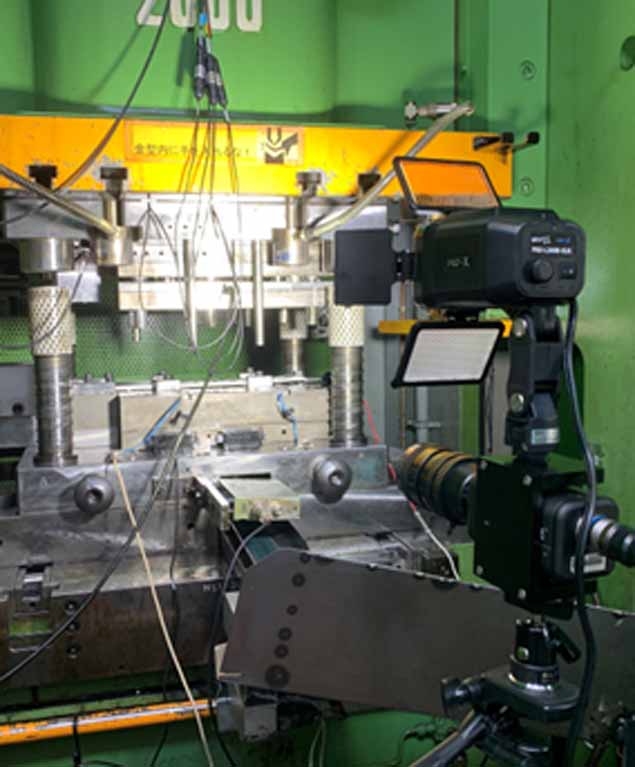
Year 2022
PRMS SHOT (Press Remote Monitoring System)
Raspberry Pi-based press operation monitoring and error detection and logging system.
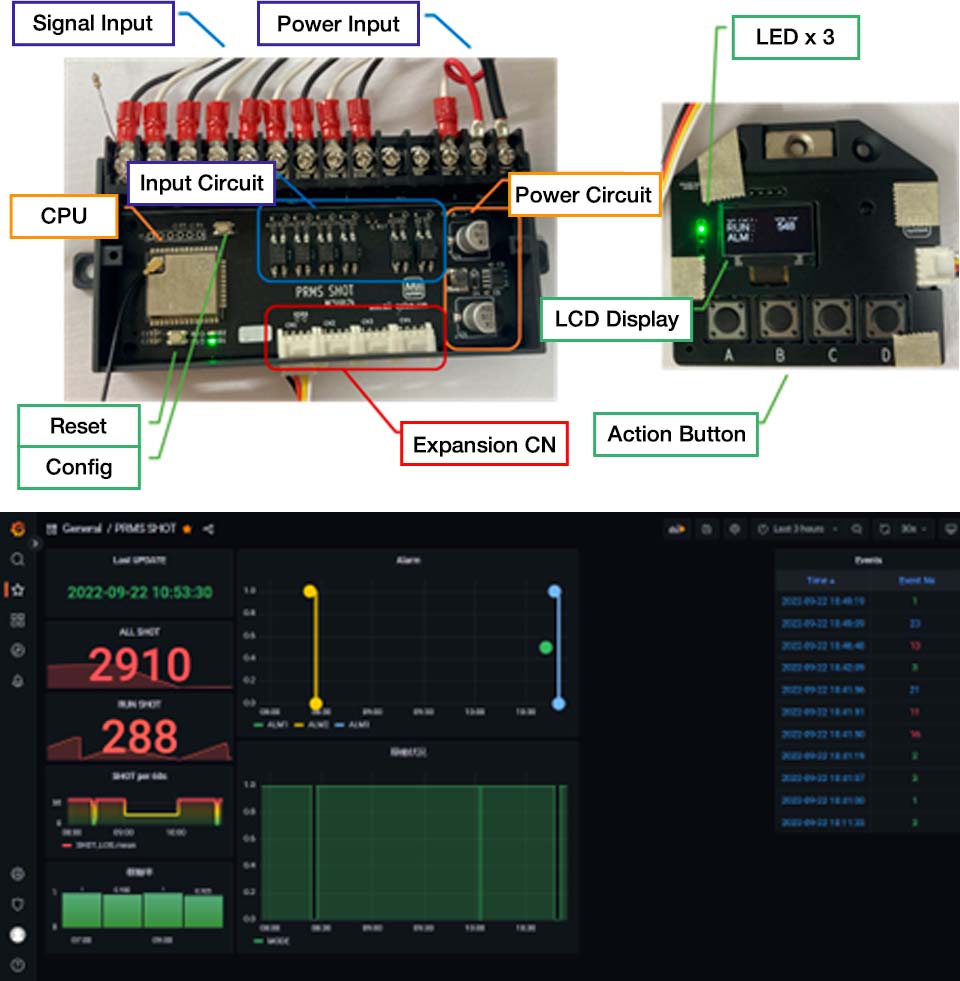
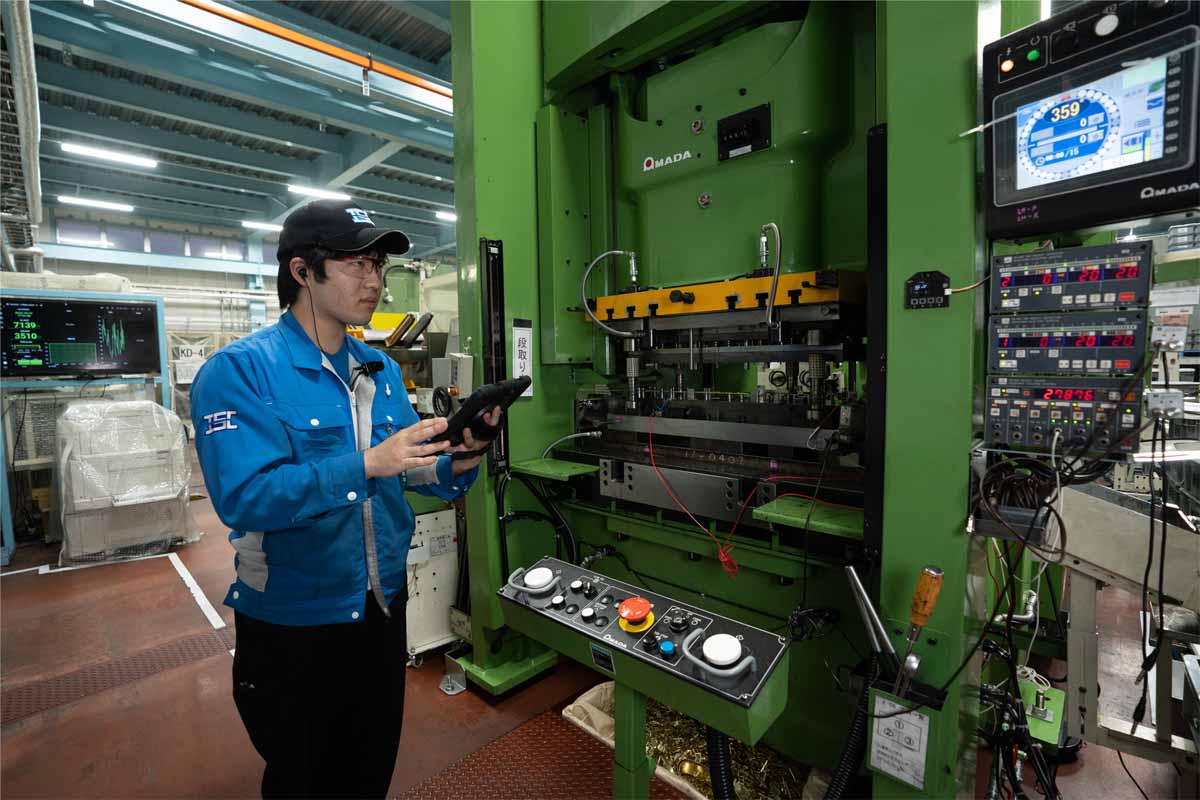
PRMS OIL (Press Remote Monitoring System)
Flow control system for press lubricant using originally developed sensors and Raspberry Pi.
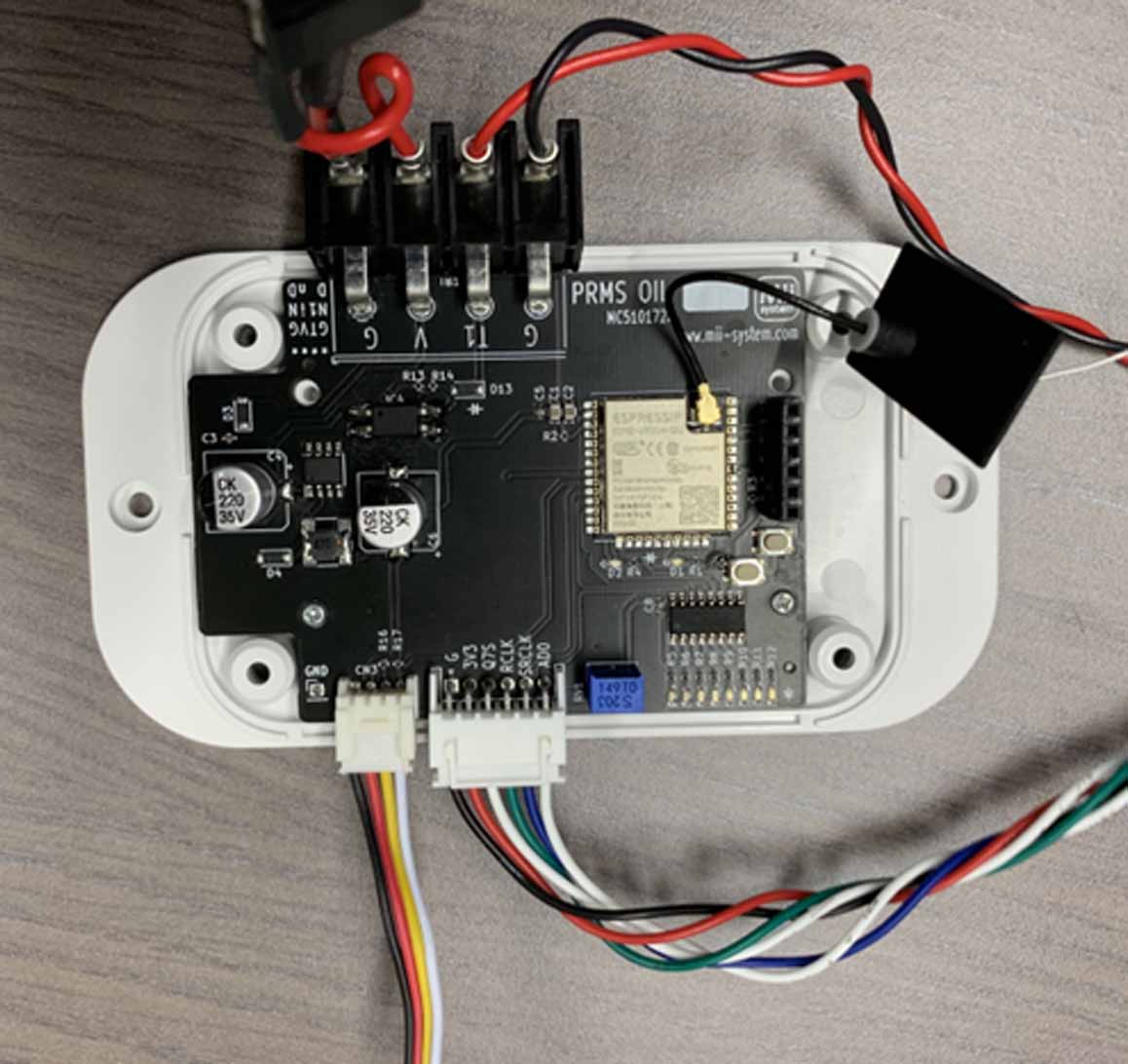
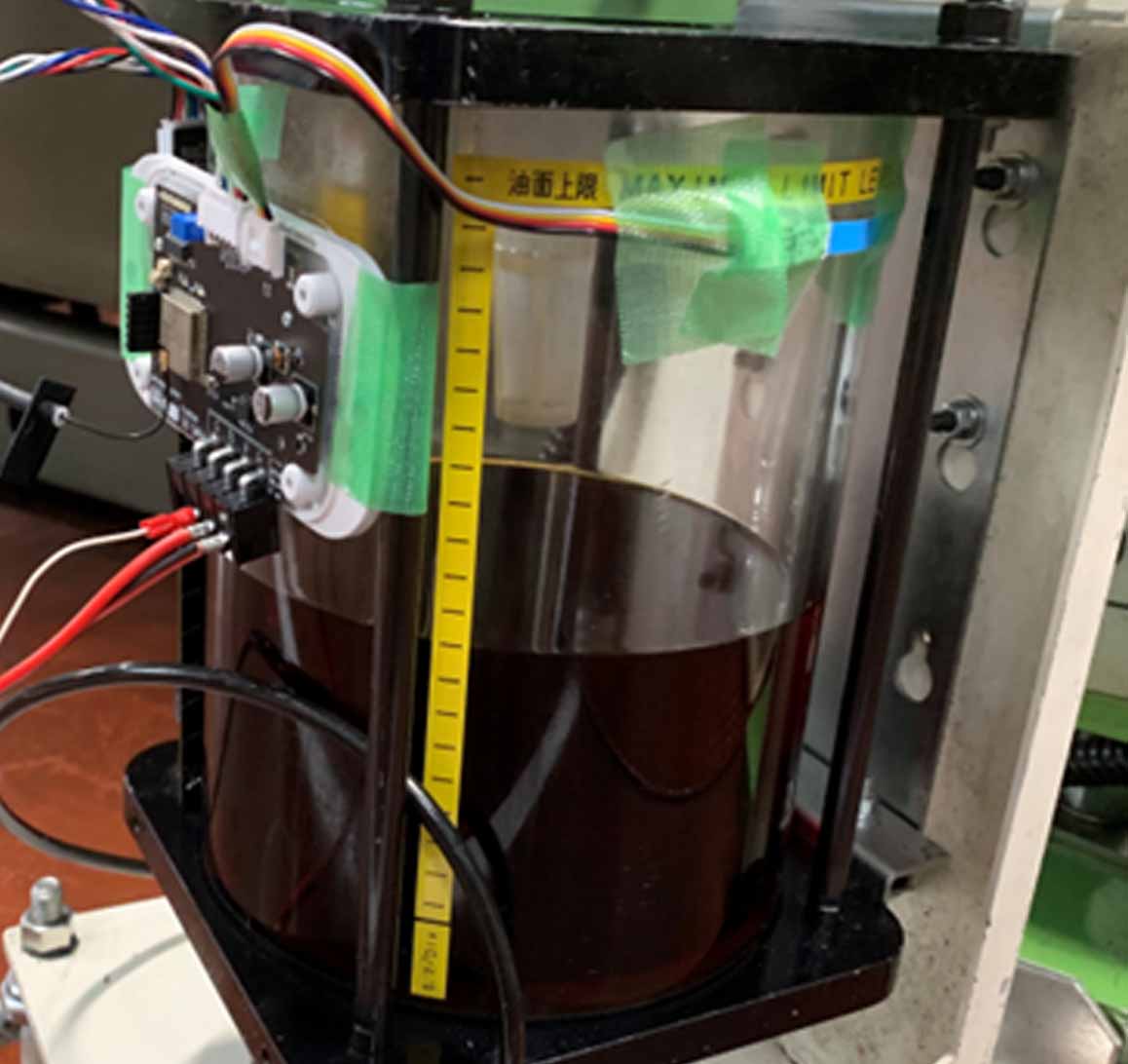
This is currently under development as a prototype.