We have over 100 press machines and a permanent die set system
We have a total of more than 100 press machines, more than 40 of which use the permanent die set system.
What is the Permanent Die Set System
By using dedicated and automated press machines for parts, we can reduce die setup time, save manpower, stabilize quality, improve die life, and increase production capacity.
Equipment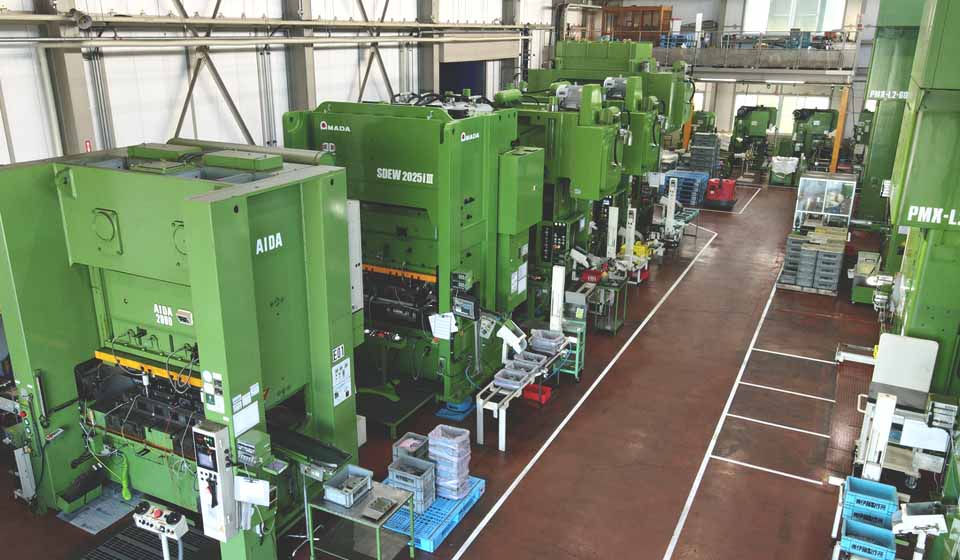
We produce 135 million pieces per year
We manufacture 135 million parts annually, mainly automotive-related parts, and delivers them to manufacturers around the world.
※ This is the actual performance for the year 2022.
Please leave the stable supply of high-quality pressed mass-produced parts to us.
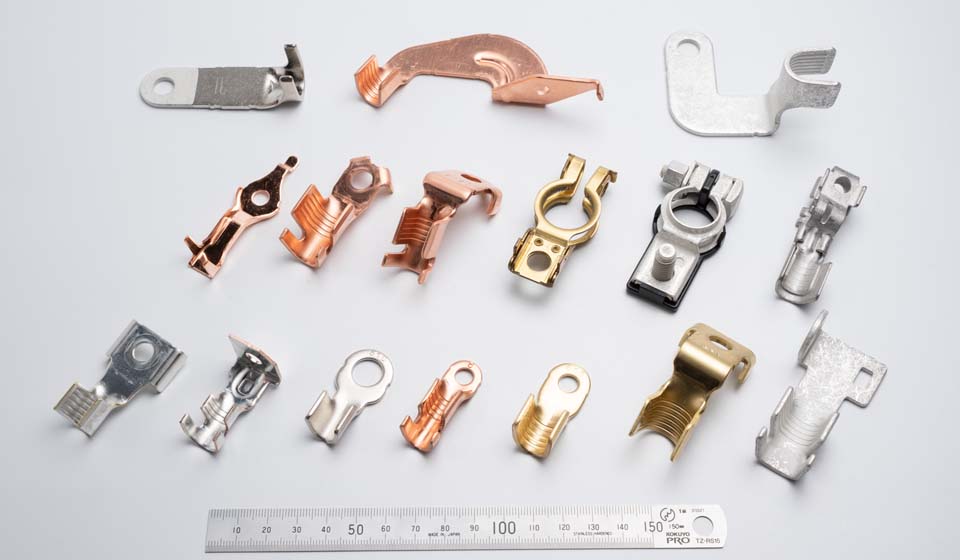
We specialize in high value-added products, such as plate forging and precision shearing
We continuously provide high-value-added products in the automotive parts manufacturing industry by developing new technologies, reducing costs, and shortening delivery times through our sheet forging and precision shearing technologies and by switching from cutting to pressing. We will continue to develop new technologies in the future.
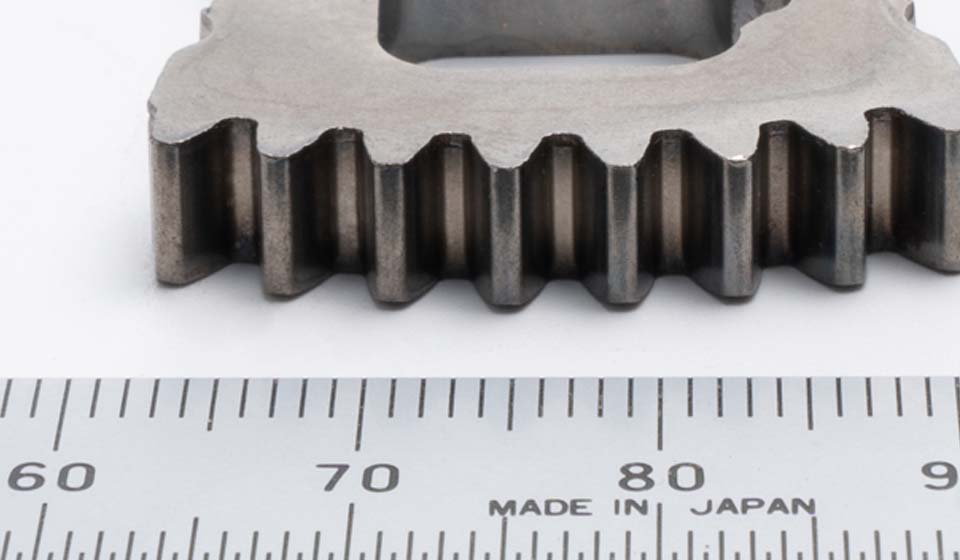
High-level global production system
Our three bases in Japan, Philippines, and Indonesia provide one-stop service from progressive die design and fabrication to press work. We have established a high-level global production system by standardizing world-class technology, quality, and facilities.
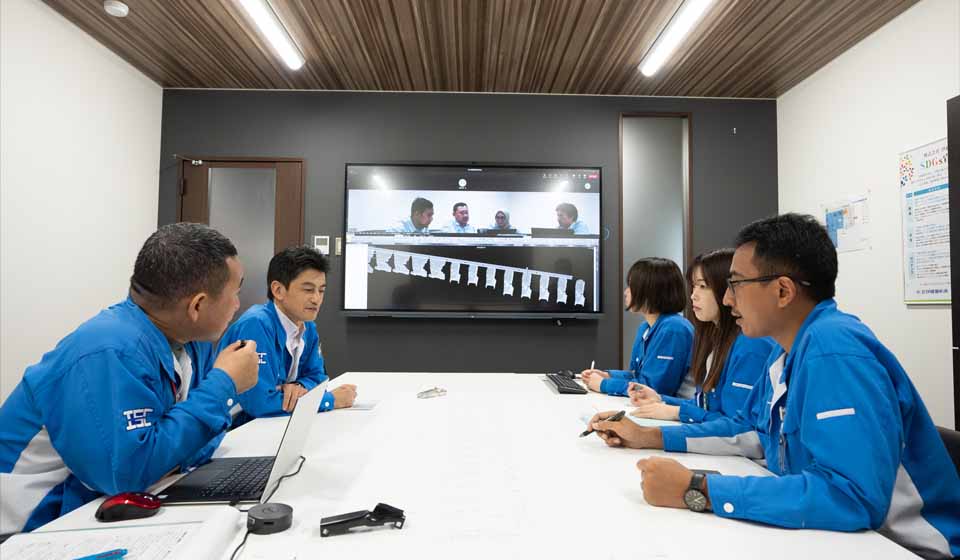
Quality control for automotive industry conformity
We have established a quality control system that conforms to the automotive industry, focusing on critical safety parts for automotive components. We have a full range of quality assurance facilities and are capable of full inspection and traceability.
Certified under ISO 9001 and Eco-Stage 2
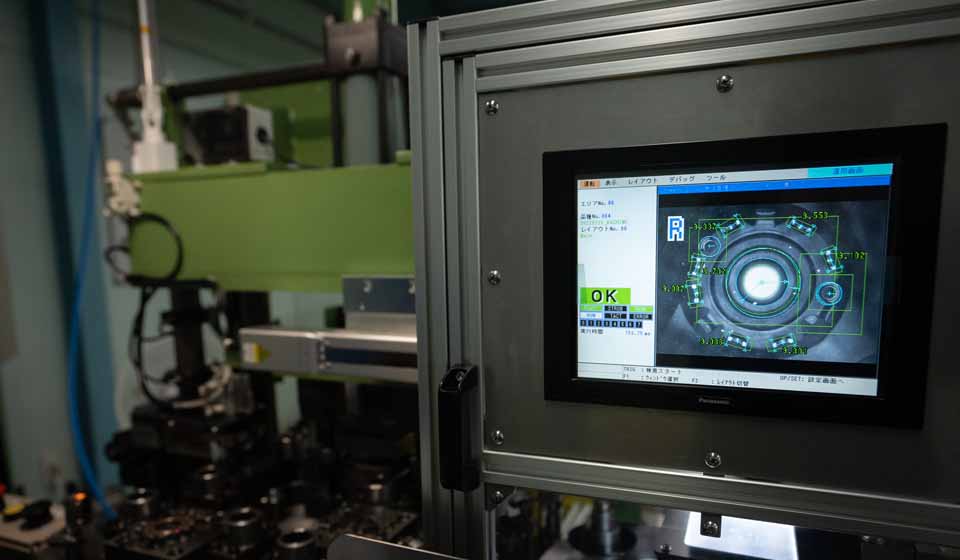
Thorough automation, IoT, and digitalization
For more than 50 years, Ito Seisakusho has built a production system based on the theme of reducing labor and has incorporated a variety of systems.
We have implemented various automation and manpower-saving initiatives, such as automatic scrap collection by conveyors, automatic box changing systems for press parts, box packing by robots, and image inspection systems. In recent years, we have been actively incorporating IoT and digital tools, such as press remote monitoring systems and press sensing systems, to further improve productivity.
-
Automated scrap collection by conveyor
-
Automatic box changing system
-
In-house developed IoT system
-
Press remote monitoring system
-
Automation from caulking to image inspection realizes manpower saving